|
1923 Ford Dealers
Handbook
Every Ford Dealer was furnished with a small booklet which detailed the features and details of the Model T, the TT
and the Fordson Tractor. Included were the prices and work sheets for the dealer to add the freight and taxes to the
factory price, as well as hints and suggestions on methods of selling the Ford line. Following is what was contained
in the Ford car section of the 1923 issue of this booklet.
|
Ford, The Universal Car |
QUANTITY PRODUCTION
Depends on absolute accuracy in the manufacture of each individual part that goes into Ford Products.
Each part—whether it is made of steel, cloth, or rubber—must conform to definite specifications
in both minute measurements and standard quality. A staff of expert chemists and metallurgists, working with modern
equipment, delicate testing devices and elaborate machinery provides those specifications.
As parts go through the many stages of manufacture in the Ford shops, from raw material to
completed units, they are closely inspected and tested after each major operation.
So that when a Ford Product passes into the possession of the user, he is assured of a product
which is as near mechanical perfection as highly trained men can make it. |
Important Sale Factors |
Following are the important factors which will show the prospective purchaser how the Ford
car will meet his requirements best.
Power
The engine develops 20 H. P.—as much as ever needed, and is always efficient and durable.
The Ford engine is driving nearly half of all the cars in the world today.
Endurance
Four out of five Fords built in the last fourteen years are still in operation. Over five million
owners throughout the world are proving its endurance. This, and its ease of operation, is evidenced by its ability
in every day use to give constant and uninterrupted service under every condition of load, road, and weather.
Simplicity
The control and operation is so simple that anyone can learn to drive a Ford in a short time.
The simplicity of the engine design and running parts means fewer parts out of order; hence fewer repair costs.
The design can be quickly understood by anyone and permits ease of adjustment.
Economy
A Ford weighs several hundred pounds less than an ordinary car with equal power and carrying
capacity, which reduces wear and tear on tires. The simplicity of the engine means economy in manufacture and low up-keep
and repair cost. The total number of all parts in the Ford Chassis retail at approximately 15% more than the price of
the complete chassis, and official figures show less than 15 cents per car for parts replaced under the factory
guarantee of defective parts.
Service
Thirty-three thousand dealers and service stations throughout the world give Ford owners
international service. A $50,000,000.00 stock of parts in the hands of dealers and branches insures Ford owners
against any hold-up for lack of replacement parts. Flat rate labor charges are used by Ford dealers. |
Better Cars at Lower Prices |
Ford cars are always low in price.
Ford cars are always high in quality.
The present selling prices of Ford cars have been made possible through:
1. Sales of a million cars yearly, which permits quantity production on the most economical basis.
2. Standardizing on one model over a period of years has made it possible to develop automatic machinery for
producing parts in quantifies at a great saving in labor costs.
3. The consumption of raw and finished products at a cost of approximately one million dollars per day, makes their
purchase contracts most attractive to manufacturing concerns, and insures their obtaining the best quality in materials
at the lowest possible cost.
4. The financial strength of the Ford Motor company not only greatly increases buying power, but also permits taking
full advantage of market conditions. The company has no bonded indebtedness to meet and its resources are always
available for use in the development of the business. |
Recent Improvements |
Front License Bracket
A new design front license tag bracket has been made standard on all cars. These brackets,
together with the standard rear brackets, are in locations convenient for attaching license tags for any state and reasonably
protected from splash and mud in service.
New Jack—Ford Design
The new Ford design jack gives to the owner at once a simple, powerful jack at a reasonable cost.
The jack is of an improved screw type, combining those features which have been in service and proved themselves to be
entirely satisfactory. The action is simple, the design is rugged, and there are few parts to get out of order.
Crankcase Front Bearing
Crankcase front end bearing has been re-designed, making it simpler and at the same time
providing greater flexibility for the front spring, with improved riding
qualities.
Spring Hangers
The new one-piece spring hangers are a decided improvement. Being in one piece they cannot
loosen or rattle in service and their permanent alignment means better spring action and better riding qualities.
Ford Design Cut-out
The new Ford cut-out has been designed with special reference to:
1. Reliability
2. Simplicity
It is very compact, of comparatively few parts, and with ample insulators.
Ford “H” Headlamp Lenses
The new Ford “H” Headlamp Lenses give to Ford owners a lighting equipment second to none on
the road. Equipped with the special design refracting type lens, and a new 21-candle-power, gas-filled, double-filament
bulb, these headlamps afford at once ample and well-distributed road light and no glare.
Steering Wheel
The steering wheel has been increased to sixteen-inch diameter, making steering and driving
in general easier, more positive and more comfortable.
Spare Tire Carrier
An improved design which combines light weight with increased strength and rigidity.
Wiring System
The wiring system has been completely re-designed, making it practically proof against short
circuits and fire. Moreover, the new design has been approved by the fire insurance underwriters and all Ford cars
equipped with the new wiring system obtain a remarkably low fire insurance rate.
1. All wires of No. 16 gauge or heavier insuring freedom from breakage and ample mechanical strength.
2. All rubber or braid insulation of standard National Electrical Code specifications approved by the underwriters.
3. Improved dash and frame clips for carrying wires. Re-designed for rigidity and strength, without danger of shorts.
4. Special insulator looms and frame brackets for heavy duty starting cables.
5. Special tail light wire suspension with tension spring and frame insulators.
6. New design dash terminal block of Fordite insulation.
7. All wires in black glazed cotton looms, giving strength and good appearance.
8. Special brackets for supporting gasoline tank to prevent contact with wiring system or abrasion on frame.
9. Special loom extension on commutator wires and fiber insulators on commutator case.
The new wiring at once insures the Ford owner against breakage, short circuits or other
trouble in his electrical system and affords him a fire insurance rate as
low as many high priced cars on the market.
Pressed Steel Muffler
The present muffler is of full, pressed steel design. Its muffling action is the equal of, and
its freedom from breakage and extra weight far superior to that of the conventional type with cast ends and brackets.
Mounted directly upon the exhaust pipe, a very compact, light and rigid construction is obtained.
The new muffler has been approved by the engineers of the fire insurance underwriters, which
means that it is free from possibility of breakage, leaks or other fire hazards.
Pistons and Connecting Rods
Pistons and connecting rods have been re-designed, providing lighter structures, without
decrease in strength or wearing qualities. This reduction in reciprocating weight has produced a smoother running motor
with reduced vibration and with quicker, snappier pick-up. Moreover, careful weight selection of these parts in the
shop before assembling into any given motor further insures deceased vibration and increased efficiency, under all
conditions of operation.
One-Piece Running Board Brackets
The new design running board brackets are of channel section and in one piece, extending
completely across the chassis.
This design insures the owner exceptional rigidity.
Fan Assembly
The new fan assembly provides the following features:
1. Large diameter pulleys preventing slippage, and increasing life of belt.
2. Bronze bushings running in self-contained bath of oil.
3. Dustproof enclosure.
Starting Switch
The new Ford design starting switch combines all the best features of manufacture and
operation of the previous types. It is simple, direct acting, of few parts, and exceptionally easy of assembling
and repair. Although there is practically nothing to get out of order in this simple switch, still disassembling
is easily accomplished by the removal of two screws, when the top lifts off and the entire inner switch is exposed.
The new switch is water, dust and rust proof, and in addition it is located in a protected
position under the floor boards.
Dash Weather Trough
Prevention of rainy weather trouble due to water on the dash and coil terminals has been
effected by application of the new design dash weather trough. This trough catches any water, which in severe rains may
work under the hood at the dash, and carries it to either side, eliminating danger of shorts, hard starting or irregular
firing, due to possible water shorts on the coil terminals or dash wiring
Radiator Mounting
The radiator is now mounted upon springs whereby it is afforded a limited flexibility. This
from sudden shocks and vibration.
Front Radius Rods
Fastening of the front radius rods has been improved by the use of tapered nuts in tapered seats.
This construction insures an absolutely tight initial fit and the wedging effect obtained prevents loosening under even
the most severe service conditions of load and vibration. |
Summary of Improvements in the Ford Chassis
|
New crankcase bearings and front spring clip, strengthens spring and makes spring more resilient
Drop forged drive shaft roller housing with Timken ball thrust bearing.
New head lamp lens.
Bright and dim two-filament headlight bulbs.
Timer insulator.
Improved brushes in starter motor.
Protected insulated terminal block for all wiring on dash board.
Heavy loom protection on battery wiring.
Timken roller bearings in front wheels—Demountable only.
Stronger radius rod, holds front axle rigid in exact position required.
New style fan with oil reservoir in hub.
Protected cut-out wire.
Improved Ford carburetor.
Dash weather strip.
Improved dash shield.
Gasoline line support.
Larger steering wheel, 16 in.
New style ammeter.
New crank case support and ball socket for radius rod.
Improved piston rings.
Running board supports.
Note—
The above list is only a partial list of Recent Improvements.
Ease of Operation
One of the outstanding features of the Ford car and a contributing cause of its deserved
popularity is the ease and facility with which the average driver can control and successfully operate it under
the most trying conditions. This is due to the proportioning and design of several features as follows:
1. Wheel base.
2. Gear change by means of foot pedal action instead of with foot operated clutch and hand operated gear shift lever.
3. Short turning radius.
4. Direct acting steering mechanism.
5. Possibility of quick shift from low speed ahead to reverse and back again without shifting of gears.
6. Impossibility of failure to accomplish gear shifts.
7. Ample and positive brakes.
Traffic Control
The combination of these features gives the driver of the Ford car unequaled control in
traffic, in sand and mud, and in all places where matter of control of an automobile is most critical and all important.
Quick Shift
The possibility of quick shift from low speed ahead to reverse and back again permits “rocking
the car” forward and back as can be done with no other automobile. This is usually sufficient to extricate the Ford from
the heaviest sand and mud.
No Gear Clash
Another outstanding feature is the impossibility of failure to accomplish gear shift as with
the Ford transmission there is no chance to clash gears, and the driver need not worry about not getting into gear
and thereby being caught in traffic with his engine disen-gaged.
Wheelbase
The short wheel base and small turning radius is a source of convenience many times daily
in going in and out of the garage and in maneuvering into a parking position at the curb. In turning corners, they
permit the driver to keep to his right-of-way and to avoid possible inconvenience in traffic or even accidents.
The design of the Ford steering mechanism is such that turning is accomplished without excessive motion of the
steering wheel. Further, being direct acting, less effort is required to steer the car in and out of parking places.
Foot-Control
One of the greatest control advantages of the Ford car is the facility with which gear changes
are made and the ability to control its speeds, through foot pedals and brake band action. Gear shifts are readily
made without removing the hands from the steering wheel and by automatic action of the feet, allowing the driver’s
attention to be concentrated on the road ahead, on traffic, steering or road conditions, as the case may require.
Light Weight
The light weight of the Ford car and the fact that the low speed ratio is high in proportion
to the car’s weight gives particular advantages in pick-up and negotiating heavy roads.
Service Brake
The Ford service brake operated by pedal and acting direct on the driving shaft through which
the power is transmitted from motor to rear wheels gives the Ford owner a powerful positive brake which permits quick
stopping of the car.
Emergency Brake
In addition, there is an emergency brake operated by hand lever and acting on the drums of
the rear wheels. This simple effective dual system of brakes requires little or no adjusting as compared with many
other designs, yet gives the Ford car a high factor of safety that is universally recognized. |
|
|
|
|
U.S. Ford Weights
|
Year Aug 1—July 31 |
Coupe |
Sedan |
Runabout |
1915-1916 |
1540 |
1730 |
1395 |
1916-1917 |
1540 |
1730 |
1380 |
1917-1918 |
1580 |
1745 |
1385 |
1918-1919 |
1580 |
1715 |
1390 |
1919-1920 |
1580 |
1750 |
1390 |
1920-1921 |
1525 |
1725 |
1400 |
1921-1922 |
1685* |
1875* |
1380 |
1922-1923 |
1729* |
1900* 1915# |
1535 |
* This weight of Coupe and Sedan includes starter and demountables. Other cars equipped with starter,
add 95 pounds. 55 pounds additional for demountable rims and tire carrier.
# Four Door Sedan |
Year |
Touring |
Chassis |
Truck |
1915-1916 |
1510 |
1200 |
1916-1917 |
1500 |
980 |
1917-1918 |
1480 |
980 |
1450 |
1918-1919 |
1500 |
980 |
1450 |
1919-1920 |
1500 |
1060 |
1395 |
1920-1921 |
1500 |
1020 |
1380 |
1921-1922 |
1485 |
1070 |
1430 |
1922-1923 |
1477 |
1082 |
1427 |
|
Fuel Tank Capacities
The old “round” gasoline tanks, as used on all Fords for many years, were of approximately
10 gallons capacity. These tanks were used on all touring and roadsters of earlier than 1920 make, and even on some
of the 1920 models. With these round tanks, it will be noticed that one gallon, at the bottom of the tank, takes more
than twice as much depth as a gallon near the middle.
The oval tanks are now used on all types of Ford cars with the exception of the Coupe and
two door Sedan. The capacity of this oval tank may be roughly estimated as 1-1/2” for the first gallon, and 3/4” for
each additional gallon up to nine.
The “square” tank is now used on Ford Coupes and two-door Sedans. With the square tank,
each 3/4” represents one gallon.
In the United States, the Old English Wine Gallon containing 231 cubic inches is standard. In
Canada, the British Imperial gallon of 271.274 cubic inches, is used. This means that an Imperial gallon is equal to
practically 1-1/5 U.S. gallons.
Since the gallons are different, we are giving a table of gasoline tank measurements, showing
number of gallons per inch: |
|
|
|
|
United States
|
Gallons |
Square Tank |
Round Tank |
Oval Tank |
1 |
3/4" |
1-17/32" |
1-7/16" |
2 |
1-1/2" |
2-9/16" |
2-3/16" |
3 |
2-1/4" |
3-1/2" |
2-15/16" |
4 |
3" |
4-11/32" |
3-5/8" |
5 |
3-3/4" |
5-1/8" |
14-5/16" |
6 |
4-1/2" |
5-29/32" |
5" |
7 |
5-1/4" |
6-3/4" |
5-11/16" |
8 |
6" |
7-11/16" |
6-7/16" |
9 |
6-3/4" |
8-23/32" |
7-3/16" |
Canada
(Imperial Gallons) |
Gallons |
Square Tank |
Round Tank |
Oval Tank |
1 |
6/7" |
1-13/16" |
1-3/8" |
2 |
1-5/7" |
2-15/16" |
2-5/16" |
3 |
2-4/7" |
3-15/16" |
3-3/16" |
3-3/7" |
|
|
5 |
4-2/7" |
5-13/16" |
4-13/16" |
6 |
5-1/7" |
6-7/8" |
5-11/16" |
7 |
6" |
7-15/16" |
6-19/32" |
8 |
8-1/8" |
9-5/8" |
7-15/16" |
|
|
|
|
|
|
Canadian Fordson Tractor Fuel Gauge
(Imperial Gallons) |
Gallons |
1 |
2 |
3 |
4 |
5 |
Inches |
1-11/64" |
1-51/64" |
2-17/64" |
2-47/64" |
3-13/64' |
Gallons |
6 |
7 |
8 |
9 |
10 |
Inches |
3-43/64" |
4-9/64" |
4-34/64" |
4-59/64" |
5-5/16' |
Gallons |
11 |
12 |
13 |
14 |
15 |
Inches |
5-35/64" |
5-60/64" |
6-21/64" |
6-46/64" |
7-12/64' |
Gallons |
16 |
17 |
18 |
19 |
20 |
Inches |
7-42/64" |
8-8/64" |
8-38/64" |
9-4/64" |
9-44/64' |
|
Improvements in Ford Two-Door Sedan and Coupe Bodies |
Several changes in design, as well as interior refinements, have recently been made in
Sedan and Coupe bodies, which add greatly to their comfort, convenience and appearance. The more important changes follow:
1. Upholstery for both two-door Sedan and Coupe bodies is now furnished in rich, dark brown, striped
wool fabric.
2. Floor carpets in deep brown shades to match the upholstery are furnished with the new bodies.
All the lower body trimming covering for such parts as heel board, gas tank box, bottom of Sedan folding seat, door covers,
etc., is now furnished in material to match the floor carpets.
3. Design of door and quarter upholstery panels has been improved very much in appearance and to
provide ready replacement.
4. The door check straps have been redesigned to provide finish in keeping with new upholstery
scheme and also increased strength and security.
5. Window lifters are provided which facilitate opening and closing of windows and provide for
holding the windows open at any desired position. Special felt channels and spring retainers for the operating levers
insure against looseness and rattle. Finished in black enamel and nickel plate, the new window lifters add materially
to the general appearance of the interior of the body.
6. Driver’s seat-back in the Sedan has been increased in comfort by slightly increasing size and
adding back springs.
7. Improved design of inside door pull handle in nickel plate finish is furnished on all closed
body doors, improving the interior appearance and adding much to the convenience of the operation of the door.
8. Inside window finishing strips are now furnished in steel, black enameled, insuring excellent
finish and permanency.
9. Outside pillar covers and in fact covers for all exposed wood parts are now furnished in pressed
steel design, guaranteeing first-class paint finish on these parts and freedom from checks, blisters and other defects
common to even selected wood designs.
10. The instrument board panel is of new design.
11. Outside door handles as now furnished with all enclosed bodies are noticeable for the attractive
appearance and convenient leverage in operation.
12. A roof drip moulding of an entirely new two-piece design, providing a much improved
appearance and finish, has been adopted.
13. Door bumpers on all closed jobs are of special Ford double-roller design, adapted to eliminate
all rattles and squeaks in doors. |
Summary of Improvements in the Ford Two-Door Sedan Body |
1. New upholstering throughout.
2. New outside door handles.
3. New inside door handles.
4. New window slides with ratchets to hold windows in any position desired.
5. The folding seat is upholstered on the bottom.
6. Higher back for driver’s seat.
7. Rear seat slopes down in back, giving more comfort.
8. Upholstered back of rear seat arranged so it gives much more space in car, and, therefore,
more leg room.
9. Upholstery extends up to dash board.
10. More room for driver, back of steering wheel.
11. Upholstered weather strips on door openings.
12. Reinforced door stop straps.
13. Steel brackets for back of driver’s seat.
14. Roller anti-rattler for doors.
15. Felt anti-rattler for windows.
16. Steel braces on round corner joints of rear window
frames. |
Features of the Four-Door Sedan |
Size
The body is approximately three inches longer than the two-door type Sedan, the extra length
providing additional leg room for the occupants of the rear seat.
Panels
All body panels are of aluminum with embossed moulding, the metal extending up around the
window sills and runways so that there are no wood parts exposed on the entire body. This feature insures a uniform
finish and will largely prevent checking or other paint trouble.
Height
The roof is of the soft type with artificial leather reinforced and padded, making it as
durable and substantial as the old fiber board type, and eliminating the possibility of vibration noises. The
overall height of the body is one inch less than the two-door design. With the straighter roof line the car has the
appearance of greatly increased length.
Visor
A permanent leather visor above the windshield adds greatly to the appearance of the car while
protecting the driver from the glare of the sun.
Tire Carrier
The tire carrier is of a new and improved design which permits the spare tire to set at an
angle that corresponds with the lines of the body.
Doors
The front door openings are 23-1/2 ins. and the rear door openings 24 ins, or the same width
as on the two-door Sedan. All doors are equipped with special Ford design double roller, dove-tail guides at center
as well as rubber bumpers top and bottom which tends to eliminate rattles.
Locks and Handles
Door handles are of the straight bar type made from hard, black rubber with nickel tips and
fittings. All doors are equipped with locks. Three of the locks are operated by levers from the interior of the body,
while the right front door lock is operated by a key from the outside.
Windshield
The upper sash of the windshield is adjustable either outwardly or inwardly to provide the
proper degree of ventilation. An improved design of clamp permits it to be easily adjusted and securely fastened in
any position. The lower section of the windshield is stationary, which is a factor in preventing rain from leaking into
the body.
Window Regulators
The windows in all four doors are operated by means of crank type window regulators, while the
rear windows are operated by the lever type used on the two-door Sedan.
Fittings
All interior body fittings, including window regulators, door pull handles, door latch levers,
etc., are finished in oxidized silver.
Dome Light
A dome light is operated by a switch on the right rear body pillar.
Upholstery
Upholstery material is of improved design with a fine, dark stripe on a brown background of a
shade that will not easily show dust and dirt. Silk window curtains to harmonize are provided for the rear windows.
Cushions
The rear seat cushion is 46-1/2” x 20” or one inch wider than in the two-door Sedan. The front
seat is 42-1/2” x 19” and will accommodate a third person if necessary. The front seat cushion is divided in the center,
making it necessary to raise but one-half of the cushion to fill the gasoline tank. Therefore, the driver may have the
tank filled without leaving his seat.
Seat cushions are held in position by means of dowel pins in place of the covered binding strip
used on the two-door Sedan.
6,000,000th Ford Motor Built on May 18th, ’22
"Ford Motor number 6,000,000 was lifted from the assembly line In the Highland Park Ford plant
at 9:14 A. M., May 18th," says a report from the Ford Motor Company, which adds that “just 5-1/3 seconds later number
6,000,001 was finished.”
At the present time the Ford plant is turning out 5,400 motors daily, the assembling line being
operated only eight hours a day.
On October 1, 1908, the first Model “T” was built; on December 10, 1915, number 1,000,000 left
the line, and number 5,000,000 came through May 28, 1921.
4 Out of 5 Ford Cars Still in Operation
Out of a total of 5,517,956 Ford Model “T” cars and trucks sold In the United States since 1908,
4,478,248 are still in daily service.
“That out of every five Ford cars and trucks sold to retail purchasers In the United States
alone during the past fourteen years, four are still in actual daily use, which is really remarkable when the hard
service of commercial cars is taken into consideration. This seems to forcibly confirm the popular knowledge of
the longevity of Ford cars.
“An idea of the important part played by Ford cars and trucks in the daily transportation of
goods and persons in the United States can be gained by realization of the fact that with the Ford cars now in
operation, averaging a minimum of 5,000 miles per year each, they would pile up a total of twenty-five billion
transportation miles—equivalent to more than a million trips around the world."
Low Operation Cost
“How much does it cost to operate a Ford car?”
This question is asked Ford Dealers many times a year and accurate details are lacking.
The Goodman Motor Company of Paris, Ill., had made investigations along this line and had
obtained an interesting report on a Ford Roadster driven by one of the salesmen of the Pillsbury Flour Mills, who
travels in the central part of Indiana.
The figures cover 42 weeks for a total distance of 12,193 miles or an average of 290.3 miles
a week. This is probably the average mileage covered by most salesmen.
The average weekly expense was found to be $9.75 for all items, and the average cost per mile
was .0335. The mileage average cost was distributed as follows: |
Gasoline and oil |
.0210 |
Repairs |
.0042 |
Tire trouble |
.0006 |
Storage |
.0052 |
Washing |
.00104 |
Accessories |
.00146
|
Total |
.03350 |
(Approximately 3-1/3 cents) |
|
|
|
|
|
Prices of Ford Products Since 1903
|
1903-1904 |
|
1904-1905 |
Model A—Runabout |
850 |
|
Model B-Touring |
2000 |
Model A with Tonneau |
950 |
|
Model C-Runabout |
900 |
|
Model C-with Tonneau |
1000 |
|
Model F-Touring |
1000 |
|
1905-1906 |
|
1906-1907 |
Model B-Touring |
2000 |
|
Model N-Runabout |
600 |
Model F-Touring |
1000 |
|
Model R-Runabout |
750 |
|
Model S-Runabout |
700 |
|
Model S-Roadster |
750 |
|
October 1, 1907, to September 30 1908 |
|
October 1, 1908 |
Model K-Roadster |
2800 |
|
Model T-Touring |
850 |
|
Model T-Town Car |
1000 |
|
Model T-Roadster |
825 |
|
Model T-Coupe |
950 |
|
Model T-Landaulet |
950 |
|
1909 to October 1 |
|
October 1, 1909 |
Model R-Runabout |
750 |
|
Model T-Touring |
950 |
Model S-Runabout |
700 |
|
Model T-Tourabout |
950 |
Model S-Roadster |
950 |
|
Model T-Roadster |
900 |
|
Model T-Coupe |
1050 |
|
Model T-Landaulet |
1100 |
|
Model T-Town Car |
1700 |
|
October 1, 1910 |
|
October 1, 1911 |
Roadster |
680 |
|
Torpedo Roadster |
590 |
Tourabout |
725 |
|
Commercial Rdstr |
590 |
Touring |
780 |
|
Touring |
690 |
Coupe |
840 |
|
Delivery Car |
700 |
own Car |
960 |
|
Town Car |
900 |
Landaulet |
1100 |
|
October 1, 1912 |
|
October 1, 1913 |
Runabout |
525 |
|
Runabout |
500 |
Touring |
600 |
|
Touring |
550 |
Town Car |
800 |
|
Town Car |
750 |
Delivery Car |
625 |
|
|
|
|
|
August 1. 1913 |
|
August 1, 1914 |
Runabout |
500 |
|
Runabout |
440 |
Touring |
550 |
|
Touring |
490 |
Town Car |
750 |
|
Town Car |
690 |
|
|
|
Sedan |
975 |
|
|
|
Coupe |
750 |
|
|
|
Chassis |
410 |
|
|
August 1. 1915 |
|
August 1, 1916 |
Runabout |
390 |
|
Runabout |
345 |
Touring |
440 |
|
Touring |
360 |
Coupelet |
590 |
|
Coupelet |
505 |
Sedan |
740 |
|
Sedan |
645 |
Town Car |
640 |
|
Town Car |
595 |
Chassis |
360 |
|
Chassis |
325 |
|
|
August 1. 1917 |
|
October 6, 1917 |
Runabout |
345 |
|
Coupelet |
560 |
Touring |
360 |
|
Sedan |
695 |
Coupelet |
505 |
|
Town Car |
645 |
Sedan |
645 |
|
|
|
Town Car |
595 |
|
|
|
Chassis |
325 |
|
|
|
Truck Chassis
(Effective 7/27/17)
|
600 |
|
|
February 21. 1918 |
|
April 1, 1918 |
Touring |
450 |
|
Tractor |
750 |
Runabout |
435 |
|
|
|
Chassis |
400 |
|
|
|
Truck Chassis |
600 |
|
|
|
|
|
August 16. 1918 |
|
April 1, 1919 |
Touring |
525 |
|
Tractor |
885 |
Runabout |
500 |
|
|
|
Coupelet * |
750 |
|
June 16, 1919 |
Sedan * |
875 |
|
Tractor |
750 |
Truck Chassis ** |
550 |
|
|
|
Truck Chassis ** |
590 |
|
|
|
Chassis |
475 |
|
Demountable Rims and Spare Rim Carrie 30x3-1/2 Tire all
around Open Cars |
25 extra |
* Includes starter and demountable
rims
** With solid tires
*** With Pneumatic tires |
|
|
March 3, 1920 |
|
September 22, 1920 |
Touring |
515 |
|
Touring |
440 |
Runabout |
550 |
|
Runabout |
395 |
Sedan (with starter) |
975 |
|
Sedan |
795 |
Coupe (with starter) |
850 |
|
Coupe |
745 |
Chassis |
525 |
|
Chassis |
360 |
Truck (Pneumatic) |
640 |
|
Truck Chassis # |
545 |
Truck (Solid) |
600 |
|
Tractor |
790 |
Tractor |
850 |
|
Demountable Rims (Open Cars) |
25 extra |
Demountable Rims (Open cars) |
25 extra |
|
Starter (Open Cars) |
10 extra |
Starter (Open Cars) |
15 extra |
|
# With starter and demountable rims |
|
|
January 26, 1921 |
|
September 2, 1921 |
Tractor |
625 |
|
Touring |
355 |
|
|
|
Runabout |
325 |
June 7, 1921 |
|
Sedan # |
660 |
Touring |
415 |
|
Coupe # |
595 |
Runabout |
370 |
|
Chassis |
295 |
Sedan # |
760 |
|
Truck Chassis ## |
545 |
Coupe # |
695 |
|
Tractor |
625 |
Chassis |
345 |
|
|
|
Truck Chassis ## |
495 |
|
|
|
Tractor |
625 |
|
# With starter and demountable rims
## Pneumatic tires and Demountable Rims |
|
|
January 16, 1922 |
|
January 27, 1922 |
Touring |
348 |
|
Tractor |
395 |
Runabout |
319 |
|
|
|
Sedan # |
645 |
|
October 17, 1922 |
Coupe # |
580 |
|
Touring |
298 |
Chassis |
285 |
|
Runabout |
269 |
Truck Chassis ## |
430 |
|
Sedan (2 door) # |
595 |
Tractor |
625 |
|
Sedan (4 door) # |
725 |
Chassis |
345 |
|
Coupe # |
530 |
Truck Chassis ## |
495 |
|
Chassis |
235 |
|
|
|
Truck Chassis ## |
380 |
|
|
|
Tractor |
395 |
|
|
|
|
INTRODUCTION
THE
FORD POWER PLANT |
The first model “T” Ford engine was made in 1908. It was the perfected development of Henry
Ford’s motor inventions dating back sixteen years to 1892 when be built his first little one-cylinder motor.
During those sixteen years Ford cars were made in many models, from little two-cylinder
"chuggers” to big six-cylinder, high-priced cars.
But in 1908 the crystallized result of all those years of experience and study was the model
“T,” the Ford Power Plant of today.
And since 1908, under every condition of use, in peace and war, in every corner of the globe,
the Model “T” Power Plant has not shown a weakness necessitating radical change of design. However minor improvements
and refinements have constantly been made, adding to its comfort, economy, efficiency and appearance. |
Ford Mechanical Facts |
Piston 3/4 lbs. lighter due to recent improvements
Valve spring exerts 20 lbs. under compression
Valve seat 1/4” convex profile
Valve port opening 1-5/16” in diameter
Connecting rod 7” long
All piston rings tapered .002”
Piston clearance not less than .003” nor more than .004”
Compression in cylinders 60 lbs.
Clutch pressure in high, 324 lbs.
Magnets on flywheel, 16 in number.
Oiling system on Ford known as “Constant Level Circulating Splash System.”
Radiator contains 95 tubes.
Radiator contains 57 fins.
Cooling system contains exactly 2 gallons 7-1/2 pints of water.
Radiator contains exactly 2 gallons of water.
Frame length on Model “T,” 100”
Frame length on truck, 123-11/16”
Front spring contains 7 leaves.
Rear spring contains 8 leaves. 2 and 4 Door Sedans, 9 leaves.
Motor contains 1 gallon of oil.
Differential 1-1/4 lbs. grease.
Ford carburetor has only one operating adjustment—the needle valve.
The tension on the clutch spring is 90 lbs.
Width of connecting rod bearing, 1.248.
Firing order, 1—2—4—3.
Water pressure test on water jackets on new Ford cylinders is from 40 to 60 lbs.
Cylinder head bolts are 15 in number and size 7/16 x 2-9/16”
Ford bodies receive 4 coats of paint; closed models, 5 coats.
Ford bodies are painted by what is known as “The Flowing System.”
Each coat is allowed to dry 24 hours and is sandpapered and rubbed down.
Fenders, splash pans, hoods, radiator shells and small parts are dipped in enamel and baked in electric ovens at 450 degrees.
Ford flywheel is much lighter than found in other motors. Because of the added weight of the transmission it is not
necessary to have a heavy flywheel.
Rated horsepower of the Ford motor is 22.5., S.A.E.
Cooling system is a thermo-siphon.
Battery used, 6 volt.
The maximum charging rate is 10 to 12 amperes regardless of engine speed.
Ford uses a two-unit lighting and starting system.
The lighting system is a single wire system.
Return circuit is through the metal of the car.
The starting motor torque in pounds is from 14 to 16 lbs. |
Details of Ford Engine Construction |
The Ford Model “T” motor is a 4-cylinder, 4-cycle, internal combustion, gasoline engine, with 4”
stroke and 3-3/4” bore. Valves are of the poppet type, arranged on one side of the cylinders, known as L-head
construction, cylinders are cast en bloc and water jacketed, the upper part of the crankcase containing the
crankshaft bearings, being integral with the cylinders. The water jacketed cylinder head containing the combustion
chambers is removable from the cylinder case. The engine and transmission are a unit and this unit power plant is
supported in the chassis frame on the three-point principle.
Cylinder Case
The cylinder case is an iron casting containing the four water-jacketed cylinder bores, 8
valve ports with manifold passages, valve guides, camshaft bearing bushing supports and crankshaft bearing supports.
The cylinder head containing combustion chamber is cast separately from the case and is bolted thereto by fifteen
bolts threaded into the top face of the case.
The cylinder bores in which the pistons are to slide, after the boring and reaming operations
vary in diameter from 3.748” to 3.749”. They are then rolled to a diameter of 3.750 with a special power-driven
rolling tool. This tool is a cylindrical block with small hardened steel rollers pivotally fitted around its circumference
at an angle of 12 degrees from vertical. In operation, when the tool is revolved within the bore, the small rollers
are pressed against the walls with a combination of sliding and rolling motion which produces a hard, smooth and polished
surface.
Water Jacket Tests
In the side of the cylinder case near the manifold ports are three 13/16” countersunk holes
in the water jacket, which were necessary to locating and removing the core in making the castings. These holes are
plugged with small, cupped, steel discs, peened into the counter-sink. At this point in the preparation of the case
the water jackets are subjected to a hydraulic pressure of 40 to 60 lbs. per square inch to test for possible weakness
or leaks in the jacket walls.
Valve Seating
The valve port hole is 1-5/16” in diameter and the face edge of this hole is milled to form
a countersink of 1-23/64” to 1-29/64” in diameter. This countersink is of convex profile of 1/4” radius, which
gives a hairline contact with the flat seat of the valve.
Steam Holes
In the top face of the cylinder case are five 1/4” steam holes entering different portions of
the water jacket. When the cylinder head is in place these holes connect with five similar holes in the cylinder
head jackets and allow the escape of air or steam which otherwise would form in the lower jacket in pockets,
impeding circulation. The water circulates through the three larger passages between cylinder and head jackets.
Dimensions of Case
Length —22-9/16” (outside of cylinder chambers)
21-25/23” (at main bearings)
Height—10-5/8” (variation 1/32”)
Width— 9-1/2” (at base)
Valve ports exclusive of seats—1-5/16”
Manifold ports (6)— 1-1/8” with 1-1/4” countersink 1/8” deep
Cylinder bores are 3.750” dia. and 6.752” long
Camshaft bearing support holes—Dia. of front hole 1.374 to 1.375, center 1.372 to 1.373, rear .9985 to 1.000
Diameter of valve stem guide hole—.3125 plus
Diameter of push rod guide hole—.437 plus.
Cylinder head bolt holes are 7/16” diameter, with No. 14 U.S. standard thread.
Valve Assembly
The valves are fitted at this point so that the seat will be protected from injury in subsequent
assembly operations. Valves are guided by the spindle hole in the case and are held in the seated position by a spring
encircling the guide boss in the case at one end and fixed to the valve stem at the other by a collar held by a small
pin passing through a hole near the end of the valve stem. The valve spring is 3” long and 1” in diameter, when
compressed by the washer and locking pin fixed to the valve stem, it exerts a pressure of about 20 lbs. In holding
the valve seated.
Dimensions of Valves
Material, valve stem is made of cold rolled steel and valve head of cast iron.
Diameter of head and upper edge of valve seat, 1-15/32”
Diameter of lower edge of valve seat, 1-17/64” to 1-9/32”
Width of valve seat, 3/32” ground at an angle of 45° to stem center.
Thickness of head, 3/16”
Stem diameter, .3105 to .312”
Length of upper seat edge to plane through end of stem, 4.974”
Spring collar pin hole, .110’ to .113’ diameter, and 4-19/32” from valve seat line.
Rough Bearing Capping
The upper half of the main crankshaft bearing supports are cast integral with the cylinder case.
These supports are semi-cylindrical and are lined with a bushing of high pressure babbitt metal molded by the aid of
a jig bar and held in place by lugs of the babbitt which fit into anchor holes in the casting. Caps of semi-cylindrical
shape and lined similarly with the babbitt metal form the complete crank-shaft bearing when bolted in proper positions.
Boring Main Crankshaft Bearings
The main bearings are bored in large lathes using boring bars, the cylinder case being held
in a jig making use of the camshaft bearing holes as locating points. The case is held in this manner during the
boring, as any variation of the distance between the crank and camshaft bearing affect the meshing of the timing
gears when these are assembled. The bearings are bored to a diameter of 1.248” to 1.249.” Boring bars are run through
the bearings twice to insure a smooth and accurate job. After the boring edges of the babbitt are filleted to a
radius corresponding to that on the crankshaft bearings. The babbitt extends over both ends of the long rear bearing
for this bearing must take care of the end thrust of the crankshaft.
Hanging Crankshafts
The crankshaft of the Ford engine is a drop forging of alloy steel with four crank throws
and three main bearings. The crank throws are all in one plane, that is, 180° apart, the two outside throws pointing
in the same direction and the two inside throws in the opposite direction. The small gear is keyed to the shaft by
means of a Woodruff key: it is made of steel and has 24 spiral cut teeth. The main crank bearings have radius of
3/16” machined at their edges. This takes care of end thrust and makes a stronger shaft than if the edges were cut
square. After the cylinder case leaves the boring operation, the bearing caps are removed and the .012’ liners taken
out The oil boles in the cylinder case bearing are now punched out and countersunk. The edges of the babbitt in the
case bearings are now filed with a flat rasp to an angle of 45° with the lower face of the case. The groove thus
formed when the cap is assembled acts as an oil lead for the bearing and also as a clearance to take care of the
babbitt pressed out during the subsequent “running in” of the bearings. The ends of the bearings are also filed
smooth. The center and front bearings have from 1/32” to 1/16” end clearance which allows for expansion and
lubrication. The cap is now “rocked” over the round shaft and two or more brass shims of .002” thickness are applied
until the rock of the cap shows a .004” or .005” clearance between case and cap edges. The caps are then bolted
down and the bearings are “run in” on a belting block at a speed of about 700. R.P.M. for the period of one minute.
The bearings during this process are pressed to conform to the shaft and a smooth even contact between shaft
and bearing results.
Dimensions of Crankshaft Bearings
Crankshaft, front 2”; center, 2-3/16” rear 3-1/8”
Case, front, 1-15/16”; center, 2-1/8”; rear, 3.118-.3120”
Cap, front, 1-15/16”; center, 2-1/16”; rear, 3.118-.3.120”
Principal Crankshaft Dimensions
Length, 25-5/32”
Length of connecting rod bearings, 1.495” to 1.505” on crankshaft.
Diameter of all bearings, 1.248”, also a standard undersize of .010” for main bearings and .025” for connecting rod
bearings. After the belting operation, the rear bearing cap is removed and the bearing surface inspected. If this
bearing is in good condition, the cap is oiled, replaced and bolted down with same tension as previous to removing.
Camshaft
The camshaft is a steel forging with eight ground cam surfaces. and three main bearings. The
shaft is driven by means of spiral gearing at half the crankshaft speed. The front and center bearings of the camshaft
are assembled on the shaft before insertion in the case. The bearings are split in half and are assembled on the shaft
bearings by means of a spring clip snapped around the middle circumference. The center bearing is fitted with a liberal
amount of play so that the shaft can line itself up properly. The rear camshaft bearing bushing is of cast iron pressed
into the base and reamed with a reamer guided by the two forward bushing supports. The 48-tooth camshaft timing gear is
also assembled on the shaft before fitting in the case. The gear is secured to the camshaft by means of two dowel pins
driven into dowel holes in the flange of the shaft and the web of the gear. These pins are 7/16” long and have a 5/16”
diameter at one end and 3/8” diameter at the other, the small end fitting in the camshaft flange. A 13/16” x 16 U.S.S.
thread locknut is screwed on to the shaft till the gear is firmly held against the flange. Push rods are now inserted
and the shaft with bearings and gear assembly is forced through the bearing support holes until the bearings are in
contact with their respective case holes. Play is within the limits of two and four-thousandths clearance between
meshed teeth.
Camshaft Dimensions
Camshaft length, 22-23/32”
Diameter of end bearing, .748”; diameter of middle one same as end
Length of end bearing, 1-3/4”; length of middle bearing 2-7/16”
Length of front bearing, 1.967”.
Width of cams, 7/8”
Diameter of heel of cam, 13/16”
Greatest diameter of cam, 1-1/16”
Flange diameter, 1-3/4”
Flange width, 1/4”
Dowel holes, .3120”—.3125”
Thread—big thread, 13/16” x 16 U.S.F.; small thread 9/16” x 18 S.A.E.
Push Rods
Material, alloy steel heat treated.
Length, 2-11/32” over all.
Diameter stem, .4355”—.4365”
Diameter head, 1”
Pistons and Connecting Rod
The Model “T” connecting rod is a steel forging of I-beam section with a babbitt bushed bearing
box at one end and at the other a clamp to encircle and hold the wrist pin. The Model “T” connecting rod is 7” long
between center of bearing to center of clamp hole. The babbitt bushed bearing is made in halves with removable cap
held by two bolts with castellated nuts so that it can be assembled about the crank bearing. The cap is assembled on
the rod and the bearing broached with .003” paper shims between edges of cap and rod before being assembled in the
engine. The width of the crank bearing box is 1.495” to 1.505” and the width of the wrist pin clamp is 63/64” to 1-1/64.”
The Piston
The Model “T” piston is a gray iron casting of softer material than the cylinder bore in which
it is to slide so that the piston rather than the cylinder will receive wear, it being more economical to replace
pistons than cylinder castings. The piston is made as long as possible in order that it may have a large bearing
surface, thus giving longer wear. Long pistons also avoid “cocking” due to angular pressure of connecting rod. The
diameter of the piston at the top is about .010” smaller than at the bottom, or skirt. This taper is to compensate
for expansion due to the intense heat to which the upper part of the piston is subjected. The top edge of the piston
is beveled in order to conform more nearly to the shape of the combustion chamber which is of rounded profile; this
bevel also avoids a sharp edge which might overheat causing pre-ignition.
The Piston Pin
The piston pin is a hollow shaft 3-1/2” in length. It is machined seamless steel tubing with
a notch at the middle point of its length, which provides against turning in the connecting rod clamp. The wrist pin
is hollow to obtain lightness and heat radiating qualities. Before the wrist pin is inserted in the piston, the brass
bushings are reamed to .740” to .741.” The wrist pins are then fitted in the piston with a snug fit; this work is held
to a half-thousandth of an inch.
The piston has three grooves around its circumference in which the rings are fitted. The two
rings near the top of the piston are termed the compression rings. Their duty is to prevent the escape of gas between
the piston and cylinder wall, the lower ring around the skirt is termed the oil ring, its duty is to keep excessive
quantities of oil from working its way into the combustion chamber.
Piston Dimensions
Length 3.808”—3.817”
Diameter at skirt, 3.748”—3.749”
Diameter at second ring, 3.743”—3.745”
Diameter at top, 3.738”—3.740”
Ring grooves 1/4” wide x 13/64” deep
Diameter of piston bushings, .740”—.741”
Diameter of wrist pin, .740”-.741” Length of pin 3-1/2”
Pistons of equal weight must be fitted in each engine. No more than .004” nor less than .003”
clearance is allowed between cylinder and skirt of piston, yet the piston must move freely when pushed back and forth
in the bore.
The piston rings are tapered around the circumference, the small diameter of the taper being
the side marked with a small “Ford.” When rings are applied to the piston, this punch mark should be toward the top of
the piston.
The .003” paper shims between connecting rod shank and cap are removed, thus a tension between
babbitt and crank bearing is produced when cap is assembled which provides for the subsequent running in process of
the bearings. Connecting rod caps are oiled and assembled on their respective connecting rods, clamping around crank
bearings. Bolts are tightened and locked with cotter pins. The engine is now placed on the belting block and is run
at 700 R.P.M. for about 40 seconds.
Timing
One intake and one exhaust valve are located in the combustion chamber of each cylinder in the
Ford engine. When the heel of the cam is in contact with the push rod a clearance of .022” to .032” exists between
the end of the push rod and the valve stem end. The lift of the valves in the Ford engine is 7/32.”
Firing Order
The opening and closing of valves with respect to position of pistons is as follows:
Exhaust valve opens when the piston reaches 5/16” before bottom center, the distance from the top of the piston head
to the top of the cylinder casting measuring 3-3/8.” The exhaust valve closes at top center, the piston being 5/16”
above the cylinder casting. The intake valve opens 1/16”past top center or when piston is 1/4” above top of cylinder
casting, the intake valve closes 9/16” past bottom center, the distance from the top of the piston to the face of the
cylinder casting being 3-1/8.”
Sequence of Valve Operation in Ford Motor
|
Cylinder No. |
|
Valve |
|
Operation |
|
1 |
|
Intake |
|
Opens |
3 |
|
Intake |
|
Closes |
4 |
|
Exhaust |
|
Opens |
2 |
|
Exhaust |
|
Closes |
2 |
|
Intake |
|
Opens |
1 |
|
Intake |
|
Closes |
3 |
|
Exhaust |
|
Opens |
4 |
|
Exhaust |
|
Closes |
4 |
|
Intake |
|
Opens |
2 |
|
Intake |
|
Closes |
1 |
|
Exhaust |
|
Opens |
3 |
|
Exhaust |
|
Closes |
3 |
|
Intake |
|
Opens |
4 |
|
Intake |
|
Closes |
2 |
|
Exhaust |
|
Opens |
1 |
|
Exhaust |
|
Closes |
Typical Cycle of Piston in One Cylinder of Ford Engine
Piston moves from top center down on its intake stroke. The intake valve opens 1/16” past top
center thus allowing the piston opportunity to reduce the pressure in the combustion chamber caused by the previous
exhaust stroke before opening the passage to the intake manifold. The piston travels downward drawing the gas
mixture from the carburetor into the cylinder. The intake valve is held open until the piston is 9/16” travel past
bottom center on the next up stroke. This lag of intake closure allows a greater volume of gas to force its way into
the cylinder than if the valve were closed at bottom center, due to the great inertia of the gas which travels
through the opening at 4000 to 5000 feet per minute. On the succeeding up stroke of the piston the gas is compressed
to 40 to 60 lbs. pressure, both valves of course being closed and the cylinder head gas tight. At, or slightly before,
the top center of this stroke the charge is fired and the piston is forced downward by the expansion of the gas on its
power stroke, 5/16” before the bottom center of this downward stroke the gases have practically exhausted their useful
energy and the exhaust valve is opened at that point On the succeeding upward stroke the exhaust valve is fully opened
and the burnt charge is forced out through the exhaust manifold. At the top center of this stroke the exhaust valve is
closed and the piston repeats its cycle.
Cylinder Head
The head is bolted to the case with 7/16” No. 14 U.S.S. thread bolts, 15 in all. The magneto
coil is now bolted to the radius at the rear end of the case. It is shimmed so that the distance from the crankshaft
flange to a plane passing through the face of the coil is 27/32.”
Hanging Transmission
The Ford transmission is built with the flywheel as a unit. This weight added to that of the
magnets carried on the flywheel makes possible the use of an unusually tight flywheel casting. The distance from the
magnet clamp faces to the depression in the center to which the crankshaft flange is bolted should be 13/16”—53/64.”
The flywheel and transmission assembly is bolted to the crankshaft flange with four l-3/16” x 7/16” x 20 thread Cap
Screws and is located by two pins .468” in diameter. The clearance between the faces of magnet clamps and coil core
faces should be not less than .025” or more than .040.”
The Manifolds, intake and exhaust, are bolted in position connecting to their proper ports
with copper and asbestos gaskets interposed. Studs 3/8” x 24 thread, clamp and nuts are used for this purpose.
The magneto contact point is fastened to the transmission cover by three screws and the engine assembly is completed.
Block Test
The block consists of a support for the assembled power plant, and a 20 H.P. motor with suitable
universal joint linkage to connect to the engine to be tested.
The engines are run on the block for a period of eleven minutes at a speed of 700 to 1000
R.P.M. The voltage of the magneto is tested by connecting the coil terminals to an alternating current volt meter
which should indicate 14 volts or more.
Transmission
There are four important points to keep in mind at all times:
1. That there are three gears forming the triple gear assembly which are riveted together (at the present time all a
re cut out of the one piece of steel), and whatever one gear does the other two must do also.
2. That whatever the action of the 27-tooth central or driven gear is the action of the car; that is, when the car is
standing still the driven gear is stationary, when the car is going forward in low the driven gear is revolving in
the same direction as the flywheel, but at a lower speed, in high the driven gear turns in the same direction as the
flywheel and at the same speed; in reverse the driven gear turns in the opposite direction to the flywheel.
3. That the clutch is used only in direct drive or high speed.
4. That the triple gears are only used to get low and reverse.
When the car is standing still and the engine running, the neutral position is obtained in two
ways, either:
(a) by putting the control lever in the vertical position which causes the quadrant on the
control lever shaft to press the set screw upward in the end of the cross shaft of the “T” shaped clutch shift shaft.
This in turn presses the clutch shift backwards, compressing the clutch spring. Pressure is thus taken off the clutch
discs and the small discs permitted to turn with the engine but not transmitting power to the large discs which are
fastened to the brake drum, drive plate, drive plate sleeve, universal joint, drive shaft, and rear axle.
(b) By pressing the clutch pedal half way forward, and by so doing the extension on the lower
end of the pedal presses the clevis which connects the pedal and clutch shift shaft downward; this turns the clutch
shift shaft and depresses the clutch spring the same as when the control lever is pulled back.
High
When the car is driven in high or direct, the control lever is pushed forward so the quadrant
does not come in contact with the clutch shift set screw, and the clutch pedal is allowed to come all the way back;
this permits the clutch spring to press against the clutch fingers with a pressure of ninety pounds, which in turn
presses the clutch push ring dowel pins, and by the leverage of the fingers increases the pressure from ninety to
three hundred and twenty-four pounds.
Therefore, the small and large discs are clamped together with a pressure of 324 pounds making
a direct connection with the crankshaft, transmission shaft, disc drum, small disc, large disc, brake drum, drive
plate, drive plate sleeve, universal joint, drive shaft, and rear axle.
Action in Neutral
When the operator wishes to stop the car but not the engine, he presses the clutch pedal half
way down which permits the small discs to run independently of the large ones. Now recalling Rule 2, that whatever the
car is doing, the twenty-seven tooth driven gear is also doing; if the car is standing still the stationary parts are
the wheels, rear axle, drive shaft, drive plate, universal joint, brake drum, brake drum sleeve, and driven gear.
In mesh with the driven gear are the three triple drive gears which also have 27 teeth. The dowel
pins, which are pressed into the flywheel, form the axes of the triple gears, so as the flywheel revolves, it carries
the triple gears around with it, and as the drums are free to revolve, the 27 teeth of the drive gear just mesh with
the 21 teeth of the driven gear in one revolution of the flywheel; therefore, while the flywheel is making one revolution,
the triple gears make one revolution on their own axis, no more and no less. So you may see in order to have the car
stand still while the engine is running, it is necessary that the triple gears make just one revolution while the
flywheel makes one revolution. If the triple gear makes more than one revolution, power will be transmitted to the
driven gear; if it makes less than a revolution while the flywheel makes one revolution it will transmit power to the
driven gear, but in the opposite direction.
Reverse
Driving the car in reverse is done by pressing the reverse, or central pedal, forward. In
doing so the band is tightened around the reverse drum which is the drum nearest the flywheel: fastened to this
drum is a 30-tooth reverse drum gear, which is also held stationary. In mesh with the 30-tooth reverse drum gear is
the 24-tooth reverse triple gear. The triple gears are all fastened together and what the triple gear does the other
two triple gears must do. When the 30-tooth drum gear is held stationary, the 24-tooth triple gear, which is in mesh
with it, the axis of which is fastened to the flywheel, revolves around the 30-tooth gear. But it is plain to see that
while a 24-tooth gear is revolving around a 30-tooth gear, it will turn six teeth, or 1/4 of a revolution more than a
revolution, but in order that the car stand still, the triple gear must make just one revolution on its own axis while
the flywheel is making one revolution; so, if the 24-tooth triple gear makes one-quarter more than a revolu-tion
while the flywheel is making a revolution, the 27-tooth drive gear will also make 1-1/4 revolutions, and in doing so
will force the 27-tooth driven or central gear 1/4 revolution in the opposite direction, or the difference between the
one revolution that the drive gear must make and the 1-1/4 that it does really make. Therefore, if the 27-tooth driven
gear makes 1/4 of a revolution in reverse for one revolution of the flywheel, it will make one complete revolution in
reverse in four revolutions of the flywheel. If the drive gear makes a revolution, the drive shaft will also. But in
order to get the ratio of the engine to the rear wheels there is another ratio in the axle to consider.
The drive shaft pinion having 11 teeth and the ring gear 40 teeth, makes a ratio of 40 divided
by 11 = 3-7/11. Now in order to get the total ratio of the engine to rear wheels in reverse the two ratios must be
multiplied. 3-7/11 x 4 = 40/11 x 4 = 160/11 or 14-6/11.
Low Speed
If low speed is desired the clutch pedal or the one to the left is pressed all the way
forward. In doing so a band is tightened around the center or low speed drum which is held stationary. The gear
attached to this drum has 21 teeth. The triple gear that meshes with this 21-tooth drum gear has 33 teeth. Now
remembering the action in neutral, the triple gear makes just one revolution, while the flywheel is making one
revolution. In reverse there was action transmitted to the driven gear because the triple gear made more than a
revolution while the flywheel was making a revolution, but in the case of low the triple gear makes less than a
revolution while the flywheel makes a revolution.
The 21-tooth gear being stationary the 33-tooth gear revolving around it only permits 21 of
the 33 teeth to be used. In high or direct drive the triple gears are not in action at all, the gears are all
meshed together and act as a lock and carry the transmission assembly around as a unit at the same speed as the
flywheel. In neutral the 27-tooth drive gear simply idles around the 27-tooth driven gear and there is no action
transmitted to the driven gear. These are the two extremes.
If the 21-tooth drum gear is held stationary, the 33-tooth triple gear revolves around it,
and instead of the triple gear making 1/2 revolution while the flywheel is making a revolution, it makes 21/33 of
a revolution, because while it is traveling around the drum gear only 21 teeth of the 33-tooth triple gear are used.
If the 33-tooth triple gear makes only 21/33 of a revolution the 27-tooth drive gear makes only 21/33 of a revolution;
therefore, the triple gears lack 12/33 or the difference between 21/33 and 33/33 of making a revolution on their
own axis while the flywheel is making a revolution.
The right hand pedal is the brake pedal, and when this pedal is pressed the band is tightened
around the brake drum, and being connected directly to the rear axle, stops the
car whenever the drum is stopped.
Ignition System
Parts of the High Tension Jump Spark System
The Ford ignition system is known as the High Tension Jump Spark System. It includes the
following parts:
Magneto—to provide current (alternating).
Induction Coil or Coil Units—to transform the primary (magneto) current of 8 to 30 volts
into a secondary current of 8000 to 20,000 volts. This is necessary, as a current must be provided which can jump an
air gap of at least 1/4 inch.
Commutator or Timer—(a) to close primary circuit and produce a spark in the cylinder at
the proper time to fire the charge and start the power stroke; (b) to control passage of current through different
coils according to the firing order; (c) to advance and retard the spark.
Switch—to start or stop current.
Spark Plug—to conduct high tension current into combustion chamber and provide a gap
across which it can jump so as to ignite the explosive mixture.
Wiring—to conduct current from one part to another.
The Magneto
Type—Flywheel type, rotating magnets, stationary field, alternating low tension current. This
magneto is of the inductor type, but unlike the other inductor type magnetos, the magnets themselves serve as
inductors. It is designed to be mounted on the flywheel, thereby becoming a part of the power plant. It is protected
from mechanical injury and moisture which tends to short circuit and damage it, by the same case that houses the
transmission. The coils are stationary to avoid trouble from commutation or moving contacts.
Magneto—is composed of 16 “V” shaped permanent magnets, mounted on, but magnetically
insulated from the flywheel, and sixteen coils wound of insulated copper tape, one quarter of an inch wide and .015”
thick, 25 turns to a coil, mounted on bosses on the magneto frame. The coils are wrapped with cambric, with fiber
inserts in the center, and bristol board insulating washers beneath when mounted on the bosses. The coils are connected
with the winding of consecutive coils in opposite directions.
Magnets—are mounted with similar poles of adjacent magnets together making 16 magnetic
poles each, having twice the strength of a single magnet pole, so in each revolution of the flywheel the magnetism in
the boss of each coil reverses sixteen times, producing sixteen electrical impulses, which at ordinary engine speed
produces a continuous alternating current of a much higher frequency than is used for house lighting. Because of this
fact it is possible to operate lights from the magneto.
The Coil Unit
The coil unit consists of a soft iron core, primary coil, secondary coil, condenser, and the
upper and lower bridge. The coil unit is also called an induction coil. Induction is the process by which a current
is produced in one wire by another current running in another wire, near the first but not touching it.
Construction—The soft iron core is made up of 160 to 170 pieces of No. 20 Swedish soft iron wire and well insulated
from the primary coil, which is wound around it, by a heavy paper tube in which the core is packed.
Primary Coil—is made up of two layers of No. 19 insulated copper wire, the first layer having 112 turns and the
second 110 turns. The primary coil is then impregnated in hot paraffin and rosin for 20 minutes. This cements the
pieces of wire in the core together, insulates and holds the windings of the primary in place.
Secondary Coil—is composed of 16,400 turns of No. 38 enameled copper wire, and between each two layers are three
layers of paper insulation. The coil is wrapped in two spools with forty-one layers on each spool. The reason for building
the coil in two spools is because there will not be as many volts difference between the con-secutive layers at the same
end of the coil as if it was wound in one spool. By wrapping in two spools the difference in voltage between the
consecutive layers at the same end is just half as much as if it was wound in one spool, and consequently, the thickness
of the insulation between the layers is reduced one-half and the diameter of the coil is reduced proportionately.
The secondary coil is then placed in a vacuum tank for twenty minutes at 220 degrees F. to make sure all moisture is
drawn out; then it is submerged in hot wax. A heavy piece of wax paper is wrapped around the primary coil and it is
placed within the secondary coil, making the induction coil complete.
The Condenser—is composed of two pieces of tin-foil 7 ft. long and 3-1/2” wide. One piece of this tin-foil
is placed on the other one but 1/8” to one side, with two layers of glassine paper insulation between and one
layer on top and one layer on the bottom. It is then rolled up into a roll and placed in a vacuum tank for twenty
minutes at 220°F. and then boiled in paraffin for twenty minutes, after which it is taken out and pressed, and to
each end terminals are attached. The condenser must test from three to four microfarads. The condenser terminals
have no electrical connection within the condenser. These terminals are connected in the primary circuit with one
terminal on each side of the contact points. The condenser is used to absorb the current of primary windings at the
breaking of the contact points and thus prevent it from arcing across the points, which would soon burn them. As
soon as the condenser is charged it seeks the path of least resistance to discharge or neutralize itself, which is
through the coil in the opposite direction. This causes the magnetic field about the coil to collapse very quickly.
The more rapid the fall of the primary current the greater the force of the induced current in the secondary winding.
The Upper Bridge—is stamped out of brass and to this at the terminal post end is riveted a cushion spring which
is stamped from bronze. The other end of the cushion spring contains a tungsten steel point and this end is held
from .003 to .005” from the upper bridge by a spacer rivet.
The Lower Bridge—is a copper spring by means of which the amperage can be adjusted by increasing or decreasing
the tension on the armature which is attached to the lower bridge by means of two screws. The armature is stamped
out of Swedish steel and has a tungsten steel point on the free end, directly under and in line with the tungsten
steel point on the cushion spring.
The parts are placed in coil box, with the exception of the upper and lower bridge, which
are placed on top, in their relative positions and tar from 300 to 350°F. is poured around them, holding them in
place, insulating them from each other, and protecting from dampness. The space between points is adjusted
from .029 to .031”. Coils are adjusted from 1.2 to 1.4 amperes.
The Commutator
The commutator effects the make and break in the primary circuit. On it depends the point at
which the spark plug will fire.
Parts of Commutator or Timer:roller brush or center, segments, shaft, terminals, cover. The roller is attached
to the end of the camshaft and revolved with it at half the speed of the crankshaft. The brush or roller makes contact
with the insulated contact points, of which there are four in the commutator cover. When roller comes in contact
with one of the insulated points, the coil unit connected with it becomes operative. After the roller passes over the
point, the coil unit is inoperative. The commutator cover is connected with the spark lever on steering column by a
pull rod connection. By this lever the spark is advanced or retarded.
Lubrication
The oiling system employed on the Ford Model T car is known as the “constant level circulating
splash system.” The oil is poured into the breather pipe at the right side of the front of the motor, from which it
flows over the connecting rod troughs of the crank case lower cover (leaving them full), and into the lowest part of
the crank-ease under the flywheel. When the motor is running the oil in the bottom of the crankcase is carried by the
flywheel and magnets near the top of the transmission cover. Here a portion of it drips into the funnel-shaped upper
end of the oil pipe where it flows by gravity down to the timing gears, returning once more to its original position
under the flywheel. The oil pipe mentioned is the only one used.
No pump is required in the Ford system. All moving parts of the motor are kept well oiled
by this system. The only opening into the crankcase is the breather pipe. Any oil which may be “pumped” to the
top of the pushrods is automatically drained back Into the crankcase by two small holes, just inside the valve door.
The Ford oiling system is highly efficient, has proved satisfactory over a long period of years, and is more
fool-proof than any other in use today. The only attention required, other than replenishing the oil supply from
time to time, is to wash out the crankcase every 750 to 1,000 miles.
Radiation
Radiator
It is light in weight, strongly built, an efficient cooler, and is easily repaired. It permits
an easy circulation of both air and water. Such is the radiator on the Ford Model “T.” The use of a large number of
small tubes fitted into a series of flat strips of sheet metal (or fins) makes a core which is more substantial and
more efficient than the almost obsolete type of large tubes surrounded by helical fins. The top tank and sides of the
Ford radiator are covered by a shell of black enameled sheet steel which enhances the appearance of the car, and has
a more durable finish than would be possible were the enamel applied directly to the radiator proper. Thisis simply
slipped on, and held in place by the two bolts which hold the radiator to the car frame’s side members.
Construction
The parts of the Ford radiator are: filler cap, filler cap gasket, filler flange, top tank top,
top tank front, top tank back, upper header top tank top reinforcement angles, splash plate upper water connection,
overflow pipe, overflow pipe straps, hood rod socket; hood rod socket washer, side walls, fins, tubes, support, lower
header, bottom tank, bottom tank brackets, lower water connection.
The radiator core or body conists of 95 tubes 1/4” in dia., 17-3/8” long, and 0.005” in
thickness), 87 fins, radiator support, and the lower header. When the core has been assembled it is placed on a conveyor
which carries it through an oven at 425°-450° F. This temperature is sufficient to melt the solder on the various parts
bf the core, thus automatically soldering them rigidly in place; Both water connection, hood rod socket, and radiator
support are tinned to prevent their rusting when in contact with the water.
Efficiency
The fins of the latest Model “T” radiator present a combined radiating surface of 54.63 sq. ft.
The 95 tubes expose to the air an additional area of 8.94 sq. ft. Thus we find that we have a total radiating surface
of 63.57 sq. ft. A better comprehension of this area can be had if we consider it as the area of a plate 8 ft. wide and
8 ft. high. All this is accomplished in a radiator core 19” long, 2-5/8” in breadth, and 17-3/8” high.
The 95 tubes of the Ford radiator hold 70.58 cu. in. of water or 17% of the water in the
entire radiator. Each cu. in. of water in the tubes has a radiating area of 113.6 sq. in. Of the 3 gallons of water
in the Ford cooling system 2 gallons is in the radiator; the remainder is in the water jackets of the motor and the
two pipes leading to them.
The Chassis
The Frame
Construction and Material Used—The frame is made up of two long straight side members, and
front and rear cross members. Side members are made of channel section pressed steel. Front cross member is bent
down to form a support for the semi-elliptic transverse spring. Rear cross member is bent upward to fit the arch of
the rear cross spring and to add more strength.
Dimensions—Length of side members of the Model “T” 100 inches.
Length of side members of the Model “TT” 123-25/32inches.
Width of front cross member of Model “T” 23 inches.
Width of front cross member of Model “TT” 23 inches.
Width of rear cross member of Model “T” 25-1/8” to center line of bracket holes.
Width of rear cross member of Model “TT” 32-5/8” to center line of body bracket holes.
Method of joining parts—Hot riveting.
By this method the rivet contracts as it cools, thus filling the hole in frame.
Brackets—These are used to support the body, running boards, truss rods, fenders, lamps,
control rod quadrant. They are fastened to the frame by rivets, excepting the fender and lamp brackets, which are bolted.
Truss Rods—Purpose-—To give added support to the frame. Are used on running
board brackets.
The Rear Axle
The most Important parts of the rear axle are:
The universal joint
The drive shaft
The drive shaft housing
The drive shaft roller bearing housing
The drive shaft pinion
The differential drive gear
The two axle shafts
The two hub brake camshafts
The two-hub brake pull rods
The two hub brake shoes
Right half rear axle housing
Left half rear axle housing
Universal Joint
The universal joint consists of a male and female knuckle joint which are assembled in two
rings—riveted together; when assembled this forms a link in the train of power transmission through which power can be
sent at any angle not exceeding 45°. The male knuckle has a square end which slips into a square hole in the transmission
drive plate assembly. The ball joint acts as a housing for the universal joint and holds it rigid and, at the proper
distance from the transmission. The female knuckle of the transmission fits over and Is pinned to the square end of
the drive shaft.
Drive Shaft
The drive shaft is 1.062 to 1.063 inch in diameter x 53-5/8 to 53-3/4” long. On the upper
end it is square and tapers at the other end about 1.” It runs through the drive shaft housing or torque tube to
the differential assembly in the rear axle housing. The drive shaft pinion gear is keyed to the tapered end and
drawn up by a 5/8” x 18 thread castellated nut and cotter pinned.
There are three bearings on this drive shaft. First, the babbitt bearing at the forward end of
the drive shaft, just back of the universal joint. This babbitt bearing is placed there because there is very little
wear or bearing strain at this joint. In reality this bearing is simply a guide bearing. Next there is a Hyatt roller
bearing at the rear end of the drive shaft just in front of the drive shaft pinion.
When the car is in motion there is a tendency for the drive shaft to thrust up toward the front
This is due to the fact that the drive shaft pinion is a bevel pinion and meshes with the differential drive gear,
which is also bevel. This end thrust pushes the bevel drive shaft pinion forward. Directly in front of this pinion is
the drive shaft roller bearing and in front of this the ball bearing which butts against the flange of the drive shaft
tubing.
The Assembly of the Drive Shaft
In assembling these parts on the drive shaft the ball bearing is placed on first; it is
prevented from going beyond its proper position by the shoulder which is formed when the end of the drive shaft is
finished. A thick washer is next put on the shaft so that the end motion of the roller bearing will not wear into the
ball bearings. A hardened sleeve is pressed on to the drive shaft which is the bearing surface within the roller
bearing. The drive shaft roller bearing runs within a hardened sleeve, called the drive shaft roller bearing sleeve.
This sleeve is pressed into the drive shaft roller bearing housing, so this roller bearing runs between two hardened
surfaces. The new style roller bearing eliminates the outer sleeve.
Differential Assembly
The axle shaft is in two halves. On the inside end of each of these is keyed a bevel gear
placed far enough to allow a short end for a bearing. A short distance from this end a groove is cut around the shaft.
After being keyed onto the shaft, the differential gear is pressed far enough back to allow two half rings, or circle
keys, called differential lock rings, to be placed in the aforementioned groove around the axle shaft. Then the gear
is forced forward and over the lock rings, holding them in place. This keeps the gear from coming off the axle shaft
when the wheel is tightened on the other end of the shaft.
On the back of the differential gears is left a hub which is ground to a bearing finish for
wear on the differential case. After placing the axles with the bevel gears keyed thereto in the proper place in the
differential case, the three differential pinions are placed on the arms of the spider, and the spider is placed over
the end of one shaft, which fills one half of the hole in the center of the spider and leaves the other half for the
end of the other axle shaft.
A fiber washer 1” x 1/32” is placed between the two axle shafts to prevent noise by not allowing
the two shafts to butt together. The other half of the differential case is next placed over the gear on the end of
the other shaft. The two differential gears are then placed in mesh with the pinions on the spider, and the two halves
of the case are then drawn together by three studs 3/8” x 24 threads and 2-1/4” long. Thus the differential proper is
assembled with the two axle shafts keyed thereon. The large ring gear or drive gear is bolted to the left half of the
differential case.
Roller Bearings
All roller bearings used in the Ford car are made of a high grade alloy steel of rectangular
cross section and wound in spiral form. The rollers are held in place in the races by the “cage,” which is composed
of a flat ring at each end of the bearing; these rings are held together by bars. In the case of the drive shaft
bearing, there is a bar between every two rollers, known as the high duty type. The races are made of a high carbon
steel on account of the high rate of speed as compared with the races on the axle shaft bearings, which are made of
low carbon steel, carbonized and case hardened.
The rollers are assembled in the “cage” so that the spiral runs in the opposite direction on
every other one. This condition assists greatly in the lubrication, as the oil will run to the left on one roller and
to the right on the next one, keeping the rollers and races perfectly lubricated.
The bearings used on the rear axle run inside of a split race or lining; the slot is “V”
shape to cause a continuous contact when in operation; there are projections on the lining used to locate it in the
housing and the hole in the one on the outer end of the axle is used for lubricating purposes. When the cages are
assembled the bars are welded in place.
Dimensions “T” Rear Axle
Drive Shaft Assembly
Length and diameter of drive shaft 53-5/8 to 53-3/4 x 1”
Drive shaft sleeve—inside diameter 1” x 3-1/16” long
Drive shaft roller bearing—length—2-5/8”
Thread on end of drive shaft— 5/8” x 18
Drive shaft tubing—50-1/2” long
Drive shaft tube is 49-5/16” from face to center of universal joint ball.
Drive shaft bushing—1” bore x 1-3/4”long
Differential Assembly
Hub diameter of differential gear 1.808”-1.809”
Gear case diameter—5.248”-5.249”
Diameter of gear end of axle shaft 1.062” to 1.063”
Bearing end of axle shaft 1.062” to 1.063”
Length of axle shaft—31-1/32”-31-3/32”
Babbitt thrust plates and steel thrust plates are all 3-3/4” outside diameter. Babbitt .l98”-.202”
Steel thickness .0875’-.0883” New .085”-.087”
Diameter of center hole in thrust plates 2.250”
Fiber washer—1 x 1/32”
Height of assembled differential case 3.623”-3.625”
Housing
Axle housings—26-3/4”
Housing diameter for roller bearing sleeves 2.208 to 2.211”
Diameter of bell 8.752”-8.754” inside of 9-1/4”outside.
From center of ring gear in housing to the face of housing for drive shaft tubing is 4.592”-4.595”
Brake pull rod clips are 18” from center of clips to center
of radius rod bolt holes.
Front Axle
There is three inches difference in the top and bottom measurements between the front wheels of
the Ford. Because of the inclination of the wheels they have a tendency to roll outwardly and pull away from each
other. To counteract this tendency the wheels are “toed” in slightly from the true parallel position; about 1/8” to
1/4” is the Ford setting.
Since the wheels, therefore, flare outward at the top their ability to withstand a side blow
which is nearly always applied at the lower part as in resisting a turn, is reduced. However, this is circumvented by
dishing the wheel; that is, by slanting the spokes outward at the rim. Thus the declination of the wheel is offset by
the inclination of the spokes, and the weight of the car is supported more vertically and the strains on the wheels are
reduced.
By tilting the axle backwards the axle is in a more favorable position to resist jolts and
shocks. Any shifting of the wheels from the straight ahead position works directly against the weight of the car so the
tendency is for the wheels to swing back to their original position.
The Ford axle is tilted backward at the top spring perches at an angle of five and one-half
degrees or 1/4 to 5/16” along the length of the spindle body.
The material used is Ford alloy steel. This type steel is also used in the spindles and spring perches.
Under test the Ford axle has been twisted, cold, several times without fracturing.
Heat Treating
Heat at 1650° F for 1-1/4 hours; cooled to atmospheric temperature.
Heat again to 1540° F for 1-1/4 hours and quenched in soda water.
Annealed to 1020° F for 2-1/2 hours and allowed to cool.
The tensile strength after hardening process is about 76,000 lbs. and after the drawing process
runs up to 125,000 to 145,000 lbs. per square inch. If the axle is bent it is straightened cold.
Spindles
The wheel axles or spindle assemblies are set between bosses integral with the main axle body.
A hardened steel bolt holds each in place. These bolts are drilled at their heads and provided with small dust,
caps, thus each is a combined oil cup and bolt.
The spindle assembly consists of the wheel axle, steering arm, inner or stationary cone,
also called the ring cone, the outer cone, the steel washer and hex nut. The steering arm and ring cone are tight
fits and must be pressed into place; the arm is held by a hex castle nut and cotter pinned. In order that the bolt
may not slip easily through the tie bar yoke and steering arm, the hole on the arm for this purpose is lined up
carefully after the arm is secured. The right spindle is threaded left hand and the left hand spindle the opposite way.
Heat Treating of Cones
Heat treating of all cones 1450° F. for 20 minutes. Ring cones are quenched in soda water and
then drawn in oil at 400° F. for 20 minutes. The adjustable cones are dipped in the soda water, then quickly immerse4
in the drawing oil. This results in a tougher and more substantial cone. Being adjustable they must fit more or less
loosely on the spindles, so do not have the solid backing that the larger ring cone has.
Radius Rods
These rods, or tubes, are pressed cold from sheet steel and the seam brazed, so if bent
the original strength cannot be restored by straightening. The point of fastening of the radius rods to the car is a
ball and socket joint brazed to the lower crank case.
Prom a ball on the tie rod, a rod is led to the ball arm of the steering gear. This connecting
rod is called the drag link, and it is through this rod that the spindle assemblies are controlled by the steering gear.
Formerly one of the sockets at the end of the rod was forged from the rod itself while the
other was made and brazed. Now both are forged directly from the rod. They are set at an angle of 40° to each other.
Construction and Heat Treating of Springs
The leaves are heated separately at 1560° F. for 12 minutes and each is then placed in a special
machine which bends it to the required arc and is then immediately quenched in oil. The leaf is held between two jaws
shaped to the necessary arc and while thus held is immersed in the oil. Each machine has four such jaws and the operation
is continuous. As the jaws return, bringing the leaf to the surface, they open automatically, the leaf sliding to a
container. After being shaped they are drawn in sodium nitrate at 850° F. Sodium nitrate is used since it is not
volatile at that high temperature.
After cooling they are bolted together through their centers and the clips set in position.
The clips hold the bands together and in alignment so that on a rebound, the whole spring assembly will act as a unit
and not throw the strain entirely on the first or eye leaf.
Spring Tests for Load and Endurance
The Ford spring will stand a load of 2000 lbs. before it is straightened out, and around
100,000 continuous vibrations before it will break. At 2000 lbs. each leaf is practically a straight line and
therefore rests firmly on its neighbor, supporting it along the whole length at the same weight.
The test for endurance is performed on a special machine for that purpose. The spring is
held by its ends and the center forced down and back again at the rate of 120 times per minute. Some springs have
stood as high as 130,000 vibrations, but the average is about 100,000.
The point of breaking varies from the center to practically any point of the length. Although
being pierced in the center by the drilled hole, only about one third of the test springs break at this point.
Steering Gear
The parts of the steering gear which are fastened directly to the front axle are the spindle
assemblies which are set between bosses integral with the main axle body. A hardened steel bolt holds each in place.
These bolts are drilled at their heads and provided with small dust caps, thus each is a combined oil cup and bolt.
Spindle Assembly
The spindle assembly consists of the wheel axle steering arm, inner or stationary cone, also
called the ring cone, the outer cone, the steel washer and hex castle nut. The steering arms of this assembly extend
towards the rear of the car and these arms are fastened together by a transverse rod called a tie rod. This tie rod
is moved crosswise by a drag link. One end attaches to the right hand end of the tie rod whose other end is attached
to the ball arm at the lower end of the steering column. Movement of this ball arm pulls the steering link one way
or the other, and through the tie rod and spindles the front wheels are turned.
The tie rod is of such length that when one of the front wheels is turned the other turns also,
but to either a greater or less degree than the first one. Regardless of the amount that either wheel is turned, it
will be found that lines through their spindles point to one and the same point and that this point lies in a line
drawn through the rear axle. However, a stop device located on the inside of the gear case allows the spider assembly
to revolve only a limited distance in either direction.
The construction of that part of the steering gear which is directly acted upon by the hand
wheel consists of a shell on the inside surface of which are gear teeth (36 in number). This shell is fastened to
the upper end of the steering gear column housing and remains stationary. In mesh with the teeth in this shell are
three small pinions, (12 teeth cut on each) which are mounted on a triangular plate fastened to the upper end of the
shaft extending down through the center of the steering column. The steering wheel carries another small pinion which
meshes with all three of the pinions which are attached to the steering column shaft.
When the steering wheel is turned by hand it revolves the central pinion, and in doing so
causes the three steering shaft pinions to roll around the inside of the toothed shell. In traveling around the
inside. of this shell the three pinions carry with them the triangular piece on which they are mounted, and the
steering shaft is thus caused to go through part of a revolution.
It will be realized that if it were possible it would require several revolutions of the
steering wheel and its gear to cause the three pinions to travel all the way around inside of the shell. It therefore
requires a considerable part of a revolution of the steering wheel to effect any great change in position of the
steering shaft. This seduction of motion increases the force applied by the driver to the road wheels and gives
better control of the direction in which the car travels.
Steering Gear Material
Toughness is more desired than hardness, for the whole mechanism is forced to undergo,
generally, sudden and severe shocks and any brittleness, of the parts would result in sudden breakage, the only
heat-treated parts of the steering assembly being the ball arm and gear studs and the bushing for the driving gear
shaft. The bracket which holds the column firmly to the frame of the car is of malleable iron. The metal absorbs
shocks and vibration readily, and being ductile, resists breaking to a very great extent. The gears and main driven
shaft are of cold rolled steel. The gear case or internal gear is of bronze, bronze used not only for the formerly
mentioned reasons but because it is easily and accurately machined.
Steering wheel rims are solid rubber 16” in diameter. Steering ball arm—H. R. steel; planetary
pinion gears, driving pinion gear, and drive shaft—cold rolled steel; gear case—bronze. Overall length of driven
shaft 54-5/16”. Angle to dash 39 degrees 45”. Distance of steering wheel to dash 29-27/32”. Steering post
case—pressed steel.
Brakes
Two separate and distinct brakes are provided. One of these brakes acts on a drum carried
with the transmission gearing and is called the service brake; it is of the external contracting type and is operated
by the right hand foot pedal. The other brake acts directly on the rear wheel hubs through drums fastened to the hubs
and into which brake shoes are expanded when a pull is exerted on rods which attach to the controller shaft. This wheel
brake is called the emergency brake and is of the internal expanding type.
The principal parts of the emergency brake consist of the steel drums, which are solidly
fastened to the rear wheels, and two shoes which expand inside of each of these drums. The service brake is carried
in the transmission and consists of a band which encircles the brake drum and of a foot pedal which acts to contract
the band through linkage drawn tight when the pedal is pressed.
The service brake retards the motion of the car through its effect first on the brake drum
and sleeve, then on the universal joint and the drive shaft, then through the rear axle driving gears and differential
to the axle shaft and to the wheels. The differential serves to divide the braking effect equally between the rear
wheels and in this way serves the purpose of what would be called a brake equalizer were such a device built as a
separate part of the braking system. The division between the rear wheels of the braking effect exerted by pulling
on the hand lever is not determined by any equalizing device, but depends for equal action on maintenance of correct
length of the pull rods.
|
400.72
U.S. FORD PASSENGER CAR PRICES
Date: October 17, 1922
At Condor, South Dakota |
Type |
|
List |
|
Frt. & Del. |
|
Tax |
|
Total |
CHASSIS |
Reg. RW |
|
235 |
|
62.80 |
|
6.84 |
|
304.64 |
Reg. DW |
|
260 |
|
62.80 |
|
7.44 |
|
330.24 |
SS RW |
|
305 |
|
62.80 |
|
8.52 |
|
376.32 |
SS DW |
|
330 |
|
62.80 |
|
9.12 |
|
401.92 |
RUNABOUT |
Reg. RW |
|
269 |
|
62.80 |
|
12.76 |
|
344.56 |
Reg. DW |
|
294 |
|
62.80 |
|
13.76 |
|
370.56 |
SS RW |
|
339 |
|
62.80 |
|
15.56 |
|
422.36 |
SS DW |
|
364 |
|
62.80 |
|
16.56 |
|
443.36 |
TOURING |
Reg. RW |
|
298 |
|
62.80 |
|
13.92 |
|
374.72 |
Reg. DW |
|
323 |
|
62.80 |
|
14.92 |
|
SS RW |
|
368 |
|
62.80 |
|
16.72 |
|
447.52 |
SS DW |
|
393 |
|
62.80 |
|
17.72 |
|
473.52 |
RW=Regular Wheels; DW=Demountable Wheels; SS=Self Starter
|
|
COUPE |
|
530 |
|
62.80 |
|
23.20 |
|
616.00 |
|
SEDAN |
2-door |
|
595 |
4-door |
|
725 |
NOTE: The above prices are for immediate delivery, but if the price should be increased or decreased by
the manufacturer before a car has been delivered to a purchaser, it is understood that the price prevailing at time of
delivery will apply.
NEW FORD BODY PRICES
|
Type |
|
List |
|
Frt. & Del. |
|
Tax |
|
Total |
RUNABOUT |
|
60 |
|
|
|
25 |
|
85.00 |
TOURING |
|
80 |
|
|
|
25 |
|
105.00 |
COUPE |
|
235 |
2-Door SEDAN |
|
300 |
NOTE: Ford Sedan and Coupe bodies are equipped with gas tanks, floor boards, cushions and mats.
Touring and Runabout Bodies are equipped with floor boards, rubber mats and cushions. No tops or windshields are included.
Body Prices are F.0.B. Detroit.
Orders are filled from nearest assembly plant. An extra charge will be made to cover freight
from Detroit to assembly plant filling the order. If body is shipped from assembly plant a crating charge of $10.00
each will be made on Touring and Runabouts and $20.00 on closed bodies.
Ford Truck Logic
Expert Construction on Scientific Principles
Ford engineers, in planning the construction of the truck, knew from large experience the
essential features to incorporate in order to make it a success. Reduced to the simplest terms, these essentials were
simplicity, strength, economy, service. To such an extraordinary degree were these qualities incorporated that the
popularity of the truck was assured from the time the first model appeared on the market.
Power and Strength
The builders designed it with more than sufficient power to carry a ton. The frame, the
axle, every bolt, nut and screw, in fact the entire mechanism throughout, is built for strength.
Economy of Upkeep
In the matter of gasoline and oil consumption, tire upkeep and general repair, it is the
last word in economy.
Simplicity
All owners of Ford cars are agreed that there is nothing complicated in the mechanical
details. The truck possesses this same simplicity.
Exclusive Features and
Specifications
Axles
Front axle of I-beam construction, especially drop-forged from Ford steel, insuring the
highest quality of axle strength obtainable. Rear axle also of Ford steel, and enclosed in a tubular steel housing.
The differential is of two-pinion type; all gears are drop-forgings made of Ford steel.
Brakes
Dual system. Service brake operates on the transmission and is controlled by foot pedal.
Expanding brake in rear wheel drums serves as emergency brake. It is controlled by hand lever on left side of car.
Carburetor
Float feed automatic with dash adjustment. Specially designed to give maximum power,
flexibility and easy starting, with economy of fuel consumption.
Clutch
Multiple steel disc, operating in oil.
Control
On the left side of car. Three foot-pedal controls, low and high speeds, reverse, and brake
on the transmission. Hand levers for neutral and emergency brake on left side of car. Spark and throttle levers
directly under steering wheel.
Cooling
By Thermo-Siphon water system. Extra large water jackets and a special Ford vertical tube
radiator to permit of a continuous flow of water and prevent excessive heating. A belt-driven fan is also used
in connection with the cooling system.
Final Drive
Is of the worm type, enclosed in a dust and oil-proof housing. Direct shaft drive to the c
enter of chassis; only one universal joint is necessary. A ball socket arrangement in the universal joint reduces
shocks and strains caused by the unevenness of the road.
Gasoline Capacity
Tank of 8 Imperial or 9-1/2 U.S. gallons capacity mounted directly on frame.
Lubrication
Combination gravity and splash system. Oil is poured into crank case through the breather
pipe on the front cylinder cover. All moving parts of motor work in oil and distribute it to all parts of the power plant.
Magneto
Special Ford design, built in and made a part of the motor. Only two parts to the Ford magneto,
a rotary part attached to the fly-wheel and a stationary part attached to the cylinder casting. No brushes, no
commutators, no moving wires to cause annoyance on the Ford Magneto.
Motor
Four-cylinder, four cycle. Cylinders are cast in one block with water jackets and upper
half of crank case integral. Cylinder bore is three and three-quarter inches. The Ford motor develops full twenty
horse-power. Special Ford removable cylinder head permits easy access to pistons, cylinders and valves. Lower
half of crank case, one-piece pressed steel extended so as to form bottom housing for entire power plant; air-proof,
oil-proof, dust-proof. All interior parts of motor may be reached by removing plate on bottom of crank case—no “tearing
down” of motor to reach crank shaft, cam shaft, pistons, connecting rods, etc. Ford steel is used on all Ford crank
and cam shafts and connecting rods.
Springs
Both front and rear springs are semi-elliptical transverse, all made of specially Ford
heat-treated steel. Ford springs are the strongest and most flexible that can be made.
Steering
By Ford planetary reduction gear system. Steering knuckles and spindles are forged from
special Ford heat-treated steel, and are placed behind front axle.
Three Point Suspension
Each of the Ford units is suspended at three points of the chassis. This method of suspension
insures absolute freedom from the strain on the moving parts.
Transmission
Ford spur planetary type, combining ease of operation and smooth, silent running qualities.
Clutch is so designed as to grip smoothly and positively, and when disengaged to spring clear away from the drums,
thus assuring positive action and maximum power.
Unit Construction
There are four complete units in the construction of a Ford car— the power plant, the front
running gear, the rear running gear and the frame.
Valves
Extra large, all on right side of motor and enclosed by a small steel plate.
Wheel Base
Model T Truck has a wheelbase of one hundred twenty-four inches. The standard tread for all
cars is fifty-six inches. Model T truck will turn in a forty-six foot circle.
Wheels and Tires
Wooden wheels of the artillery type with extra heavy hubs. Only tires of the highest grade
are used on Ford cars. Front pneumatic, 30 x 3-1/2”, rear wheels, solid rubber tires 32 x 3-1/2” or pneumatic
cord 32 x 4-1/2 inches.
Carrying Capacity
One ton.
Lubricant For Worm
An A-1 heavy fluid or semi-fluid is used to lubricate differential in Model T Truck.
Speed
With standard gearing, a speed of not more than 15 m.p.h. is recommended, and with special
gearing, a speed of not more than 22 m.p.h. is recommended.
Utility of the Ford Truck for the
Farmer
One Motor Truck Replaces From Six to Eight Horses
While the truck is being introduced largely because it offers cheaper hauling than horses, a
factor equally as important is its ability to do things entirely beyond the horse. It will carry twice the load in
half the time. Many trucks are carrying raw materials to factories. The absence of this service rendered would often
mean that thousands of men would go idle for lack of the material on which they work.
It Takes a Five-Acre Crop to Feed One Horse For One Year
For every horse supplanted with a Ford Truck, five acres is added to the farm. The truck will
make available for raising food stuffs the land whose yearly crop is otherwise required to feed a horse.
The Ford Truck Assists the Farmer Through the Rush Season
Where there is a shortage of labor, Ford trucks conserve by hauling grain, hay and corn. It is as
essential on the farm as the binder.
The Ford Truck Gives the Farmer More Time For Cultivation of Crops
Many farmers have been inclined to decrease the production of perishable foodstuffs, owing to
the time required for hauling to market and the shortage of labor. Lots of fruit, vegetables and other produce which
could be marketed are left on the farm to rot. The use of the truck in Rural Motor Express Lines, offers the best
possible medium through which Farmers, Truck Growers, and Dairymen may go to market; thus increasing the local food
supply of perishables.
The Ford Truck “Eats” Only When It is Working
The Ford truck has no expense for food during idle hours. It never goes lame, gets the
colic or dies.
The Ford Truck Gives the Farmer Top-Notch Produce Prices
The Farmer depends as much on rapid access to market as on the productivity of his farm.
The prices obtained for many classes of produce depends to a large extent upon placing them on the market at the
right time in good condition.
The Ford Truck Saves Shrinkage in Hauling Live Stock
The truck has many uses in farm work, one of which is the hauling of live stock to market.
A certain live stock farmer, being at first skeptical regarding the adaptability of a truck to his work, finally did
purchase one and discovered that the increased revenue obtained for his stock, because of the reduced shrinkage
in hauling them to market by truck, as against his old method, more than paid for the cost of each trip.
The Ford Truck Hauls Cheaper than a Team
The expense of operating a truck is about one-half or less than that of a team. The total
cost of operation for gasoline, oil, grease and tires will range from 6 to 10 cents per mile. Modern farmers know
enough about mechanics to operate and maintain trucks economically, and two or more farmers with not enough use for
a truck apiece can buy and operate one together.
The Ford Truck Will Give the Farmer Two Hours More Working Time Each Day
The farmer living twenty miles from town and using a truck, is just as near as one five
miles away who depends on team hauling. The truck saves two hours or more each day that would otherwise be spent
in harnessing, feeding and watering a team.
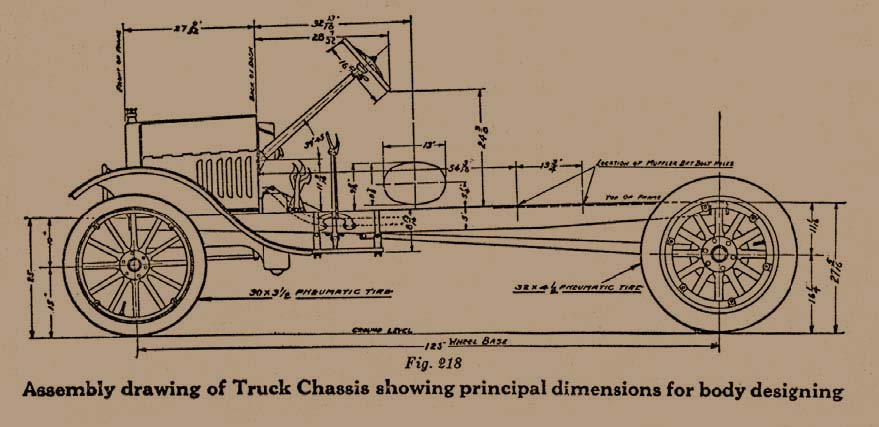
The Data Book continued with several pages of various businesses which might have use for the
Ford truck, along with possible applications in those businesses. These are not included here because of their limited
interest today.
Also there were many pages showing various methods of financing the purchase of a Ford, a list of
U.S and Canadian serial numbers, and coverage of the Fordson tractor. These, too,
are not included here.
HENRY FORD
Biography which appeared in the 1923 Ford Data Book
Born July 30, 1863, of farmer parents, representative of Michigan’s sturdy pioneers of
three-quarters of a century ago, Henry Ford’s early life paralleled closely that of other farmer boys of that day,
a round of daily chores, attending the distant district school, and the all-day’s work in the fields in summer. One
exception alone marked his boyhood; he had rigged up a shop containing a few tools of his own gathering, and there,
during spare time, his passion for things mechanical held sway. At the age of sixteen he left school and the Dearborn
farm to become a machinist in Detroit, only a few miles away.
Nights he did repairing in a watch and jewelry shop. And for eight years Henry Ford followed
this line, working in various shops, but always adding to his fund of knowledge of machinery, and preparing himself
for greater tasks.
During his 24th year, his father offered Henry Ford 40 acres of timbered land provided he
returned to the farm. He accepted the land and accordingly returned, bringing with him his shop, which boasted many
new tools. Immediately a sawmill and portable engine were obtained, and Henry Ford became a lumber manu-facturer. The
same year he happily married Clara J. Bryant, born and raised only a few miles from his father’s farm. The issue of
this marriage was an only child, a son, Edsel Bryant Ford.
With some of the first lumber from his mm, Henry Ford built on his new farm a house one and
one-half stories high and thirty-one feet square. Into this he and Mrs. Ford moved. His shop was also brought to the
new place, where he began work on a steam car. It was the first Ford passenger car, but was soon abandoned, because
though boiler after boiler was experimented with, none proved satisfactory.
He stayed on the farm two years, but again left for the city to become night shift engineer
in a lighting company at a salary of $45.00 a month. However, his general ability and genius in making impromptu
repairs, soon brought him entire charge and raised his salary to $125.00, which he earned for seven years with the
same company.
A small brick shed in the rear of his home was fitted into a work shop, and then Henry Ford,
often working far into the morning hours—devoted his spare time to creating his first gas car. It was—or is, for it
still runs—a two cylindered motor car with a speed of from 25 to 30 miles an hour. A company was formed with Henry F
ord as chief engineer, and a few cars were built. This con-nection not being satisfactory, he withdrew in 1901 to
begin building another car, which was completed in 1902. In 1903, the present Ford Motor Company was organized. Mr.
Ford owned 25-1/2% of the stock, and held the position of Vice-President and Factory-Manager. The company was
capitalized for $100,000 but not more than $28,000 in cash was ever paid into the treasury of the company.
Henry Ford soon realized that his own ideas and policies, which were very clearly defined,
could not be carried out unless he should be in free control. Accordingly, in 1906, he purchased sufficient stock
to bring his holdings up to 51%, and a short time later, at seven to one, procured 7-1/2% more, making a total of 5
8-1/2%. This arrangement continued until 1919, when Edsel Ford, who had succeeded his father as president, purchased
the remaining 41-1/2% of the stock. The company was reorganized under the laws of Delaware for an authorized
capitalization of $100,000,000, and this Is the present arrangement.
The first car manufactured by the Ford Motor Company was on the road in June and sold the
early part of July, 1903. However, no sooner had “production” begun in the Ford Plant, than Henry Ford began building
racing cars, for in the early days of the industry, practically every noteworthy automobile company entered its cars
in the races.
The first Ford racer, piloted by Henry Ford himself, won race after race in all parts of
the country. No entry list was considered complete until the Ford was in. With “999” Henry Ford first broke the mile
a minute record on an ice track at Baltimore Bay In 1904. The remarkable feats of Ford cars probably did as much to
make known the name of Ford as any other circumstance.
The growth of the Ford Motor Company has been progressive, continuous; and at all times
impelled by the personality of its founder. The present plant site contains three hundred and five aces, of which
one hundred and twenty-three are under roof; and 50,000 and more employees work
in this huge factory.>/p>
Facts on Highland Park Plant
-
It takes 665 men to keep the Ford Plant at Highland Park clean.
-
There are 32.000 windows washed each day.
-
Payroll of over $500,000 per day.
-
Most up-to-date fire alarm system in the world. 300 Fire Alarm Stations in the factory.
-
45,100,000 cubic feet of gas is produced daily.
-
3,000,000 gallons of water refrigerated each day.
-
Ford band consists of 60 pieces.
-
100 chemists in research laboratories.
Highland Park Power House
The big power building Is 150 feet wide by 400 feet in length, 225 feet from ground to top of
smoke stacks. It required 5,200 tons of structural steel (enough to erect a 20-story “skyscraper”). The huge engines are
on the ground floor boilers on third, and fuel, etc., on upper floors.
Walls and columns faced with white enamel brick, and all other surfaces painted white. T
hree 50-ton cranes, with parallel runways extending full length of building. The huge engines are composite gas-steam
type (the only ones of the kind in use), and are rated 6,000 H.P. each. (A brief description of one will answer for
all); the gas side has tandem cylinders, 42 x 72 in., and the steam side tandem compound cylinders, 36 x 68 and 72
inches. Between the two engines are mounted a 100-ton flywheel and a 4,000 k.w. 250-volt direct current generator;
the latter being of unusual size owing to a speed of 80 R.P.M. The approximate weight of this dual gas-steam engine
is 1,500,000 pounds—the steam engine weighing 700,000 and the gas one 600,000, and the generator and flywheel 200,000
pounds each. The bed on the steam side weighs 150,000 and on the gas side 140,000 pounds. the crankshaft is 25 ft. 2 in.
long and 31 in. in diameter at the bearings and 34 in. for the flywheel, weighing 72,000 lbs.; the crank disc weighs
28,000 lbs., and the connecting rod, with boxes, 10,000 lbs. The gas engine piston rods weigh 14,000 lbs. and each
piston 8,500 lbs., while the steam engine piston rods weigh 10,300 lbs. and the main cross head, on either engine,
complete with shoes, pin and box, 6,000 lbs. Over all the engine measures 32 ft. in width, with length of 72 ft.,
occupying a floor space of 2,304 sq. ft. The generator extends 14 ft. 5 in. above the floor and 11 ft. underneath.
There are nine of these gas-steam engines, and in addition, one smaller steam engine
and four great pumps.
Production Figures
The Ford Motor Company’s fiscal year dates from August 1st to July 31st. Each year’s
production figures since 1903, when the company was organized, tells its own story:
|
|
|
Ford Cars and Trucks |
1903-4 |
1,708 |
1905-6 |
1,599 |
1906-7 |
8,759 |
1907-8 |
6,181 |
1908-9 |
10,660 |
1909-10 |
19,051 |
1910-11 |
34,979 |
1911-12 |
76,150 |
1912-13 |
181,951 |
1913-14 |
264,972 |
1914-15 |
253,161 |
1915-16 |
534,108 |
1916-17 |
785,433 |
1917-18 |
708,355 |
1918-19 |
537,432 |
Aug. 1, 1919 Dec. 31, 1919 |
401,982 |
1920 |
1,074,336 |
1921 |
1,013,958 |
1922 |
1,232,268 |
Fordson Tractors |
1917 |
254 |
1918 |
34,167 |
1919 |
57,290 |
1920 |
70,955 |
1921 |
36,781 |
1922 (1st 11 months only) |
62,842 |
Production during 1917 and 1918 was materially affected by war demands. Many thousands of Ford
cars were made for army service—staff cars, ambulances and trucks. The company also produced volumes of other war
materials. Upon the signing of the armistice the United States Government gave us a citation as being a 100% war work
organization. |
|
|
|