One of the most persistent myths in
automotive history is the belief that Henry
Ford invented the automobile. This, however,
is far from the truth. The automobile was
already in existence long before Ford
entered the scene. What he did
revolutionize, however, was the way
automobiles were manufactured. His
groundbreaking innovation was the
introduction of the moving assembly line - a
method that would forever change the
landscape of industrial production.
Before Ford's innovation, cars were
assembled one at a time, often by skilled
craftsmen who painstakingly put together
each component by hand. This process was
slow, expensive, and inefficient, making
automobiles a luxury item available only to
the wealthy. Ford recognized the need for a
better way - a system that would allow for
mass production at lower costs while
maintaining quality. His solution came in
the form of the moving assembly line.
The key feature of this revolutionary system
was the conveyor belt, a mechanism that had
already been used in other industries,
including meatpacking plants. The idea was
simple yet transformative: instead of
workers moving from one station to another
to complete various tasks, the product
itself would move along a track, stopping at
different stations where specialized workers
would complete specific tasks. This approach
maximized efficiency and minimized wasted
effort, allowing for a dramatic increase in
production speed.
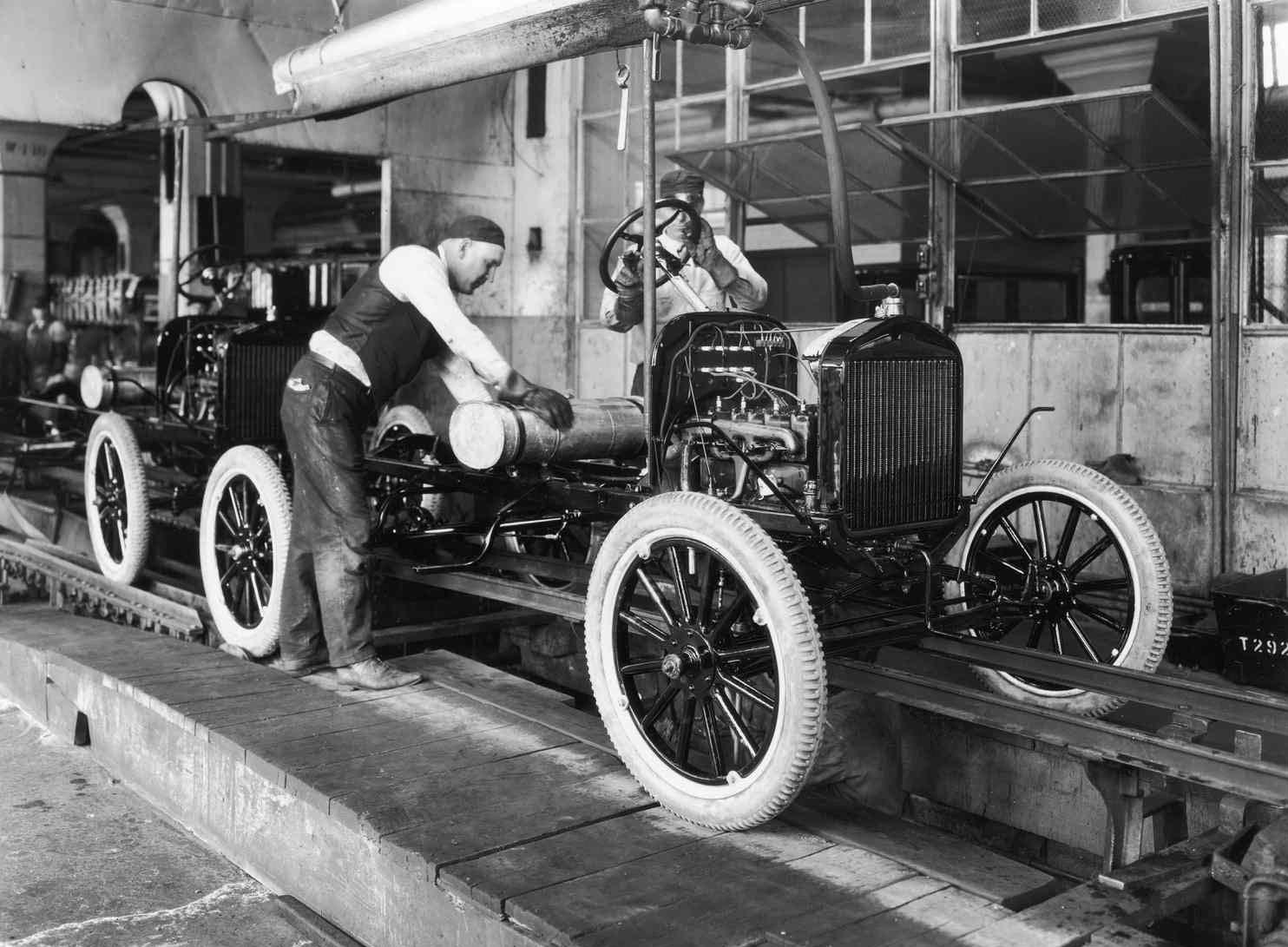 |
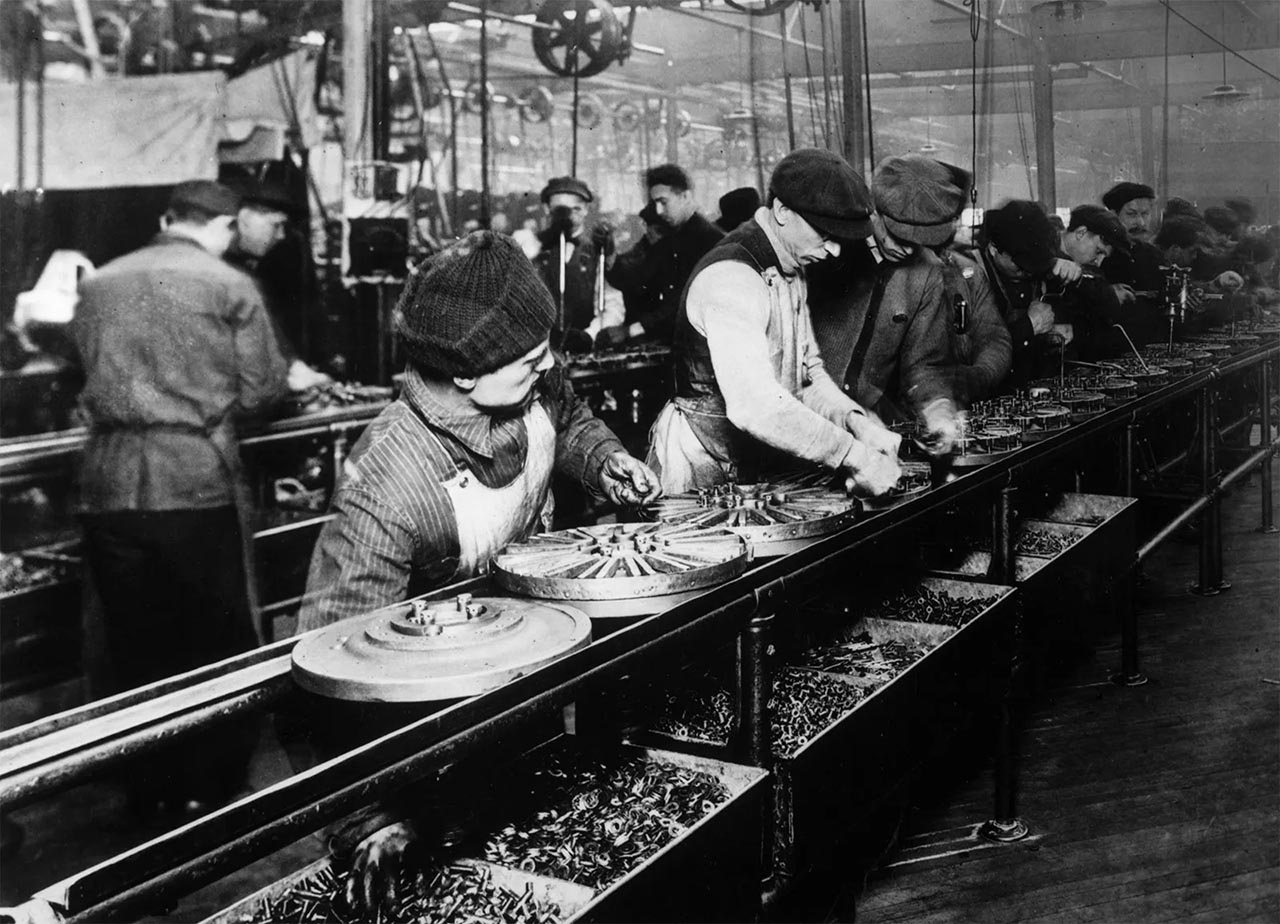 |
After extensive experimentation and
refinement, Henry Ford and his team at the
Ford Motor Company successfully implemented
the moving assembly line in 1913 at the
Highland Park assembly plant. At first, the
vehicles were physically pulled down the
line by a rope, but soon, a simple chain
mechanism took over. This seemingly small
change had an enormous impact: the time
required to build a Model T dropped from
over 12 hours to just 90 minutes. This
breakthrough meant more cars could be
produced at a lower cost, bringing
automobile ownership within reach of the
average American.
However, not everyone welcomed this new
system. While the efficiency of the assembly
line was undeniable, it introduced new
challenges for workers. Previously,
employees had been involved in multiple
aspects of a car’s assembly, which provided
a sense of craftsmanship and accomplishment.
With the moving assembly line, however,
workers were now assigned to perform a
single repetitive task, over and over again.
The work became monotonous, and strict
timing meant that employees had to complete
their tasks quickly before the car moved to
the next station. This led to increased
stress, mistakes, and dissatisfaction among
workers. Some employees found the work
unbearable and began leaving for jobs
elsewhere.
Recognizing this growing problem, Henry Ford
made a bold and unprecedented move - he
introduced the $5 workday in 1914. This
initiative more than doubled the daily wage
of his workers, from around $2.34 to $5. At
the time, many critics predicted that this
decision would drive the company into
financial ruin. Instead, it had the opposite
effect.
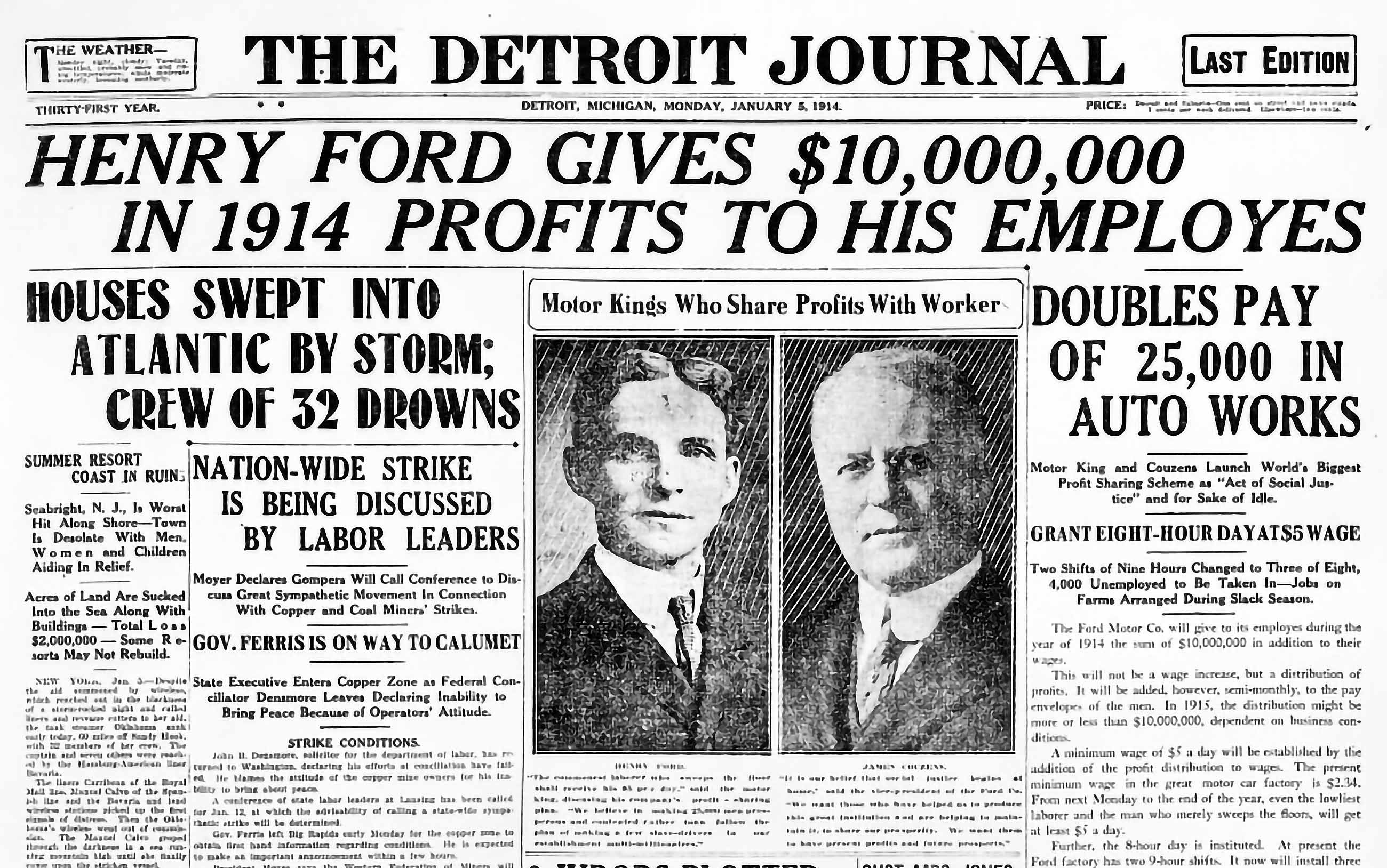
Word of Ford’s high wages spread
across the country, and workers flocked to
Detroit in hopes of securing a job at the
Ford Motor Company. The company was suddenly
inundated with skilled and dedicated workers
who were willing to tolerate the monotonous
assembly line in exchange for better pay and
improved living standards.
But Ford didn’t stop at increasing wages. He
also reduced the length of the workday.
Shifts were cut from nine hours to eight,
which not only made the work more bearable
but also allowed for the creation of a third
shift, turning Ford’s factories into
round-the-clock operations. This further
boosted production capacity and
profitability, setting a precedent for the
modern five-day workweek and influencing
labor policies across industries.
This new approach to manufacturing and labor
became known as "Fordism," a term that came
to symbolize the combination of mass
production and higher wages. Other
industries soon followed Ford’s example,
adopting similar methods to increase
efficiency and attract a stable workforce.
The ripple effects of Fordism extended
beyond manufacturing, influencing economic
and social structures throughout the 20th
century.
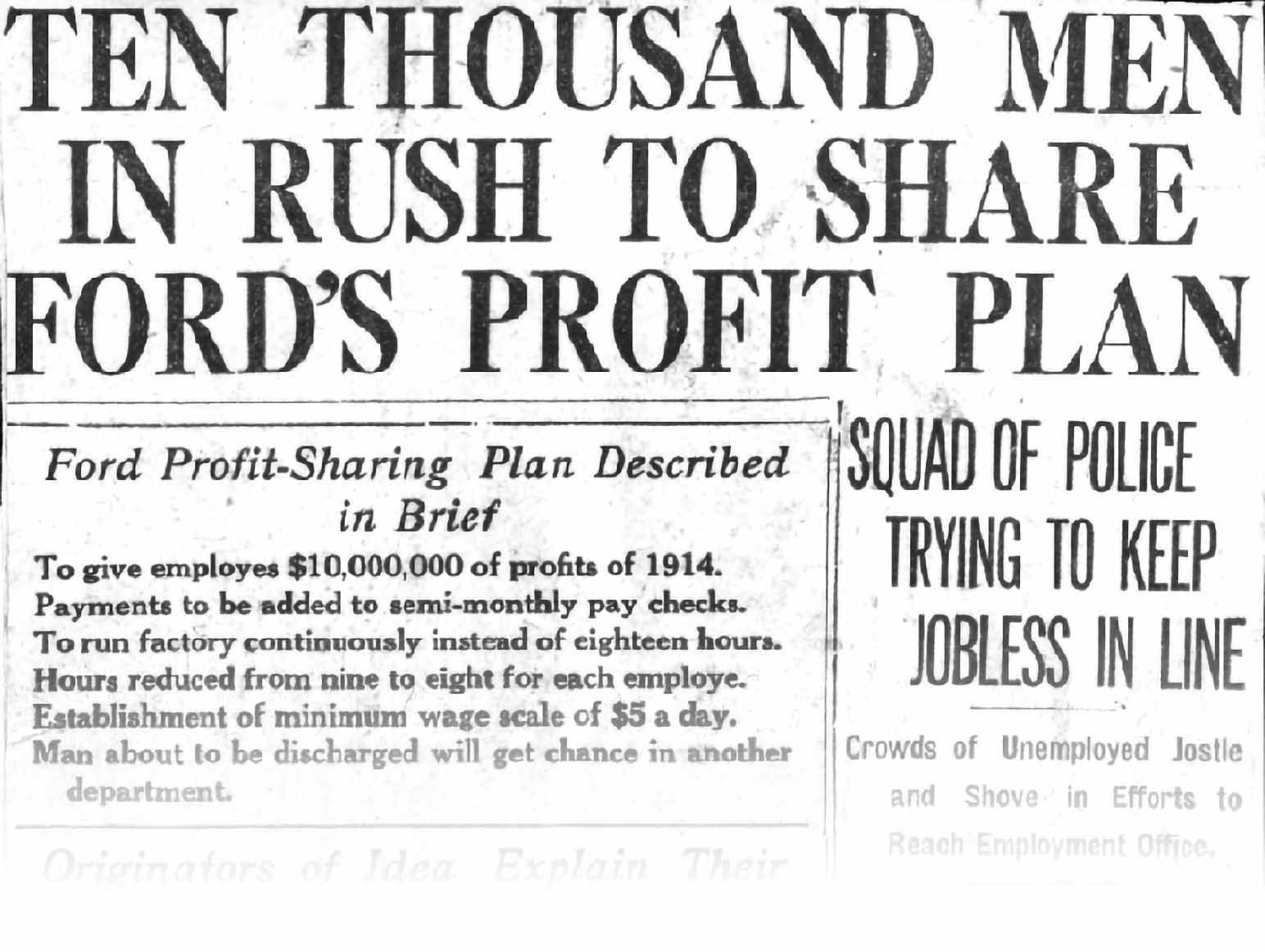
One of the most significant outcomes of
Ford’s moving assembly line was the dramatic
reduction in the price of the Model T. When
it was first introduced in 1908, the Model T
sold for $825 - a hefty sum at the time. By
1925, thanks to increased efficiency in
production, the price had dropped to just
$260. This made the automobile more
accessible than ever before, transforming it
from a luxury item into a household
necessity for middle-class Americans. Not
only could more families afford to buy a
car, but Ford’s own employees - who had once
been unable to purchase the products they
built - could now afford to drive the very
vehicles they assembled.
In the end, Henry Ford didn’t invent the
automobile, but his contributions to
manufacturing reshaped the industry and
changed the world. His pioneering use of the
moving assembly line made cars affordable
for the masses, revolutionized industrial
production, and set new standards for wages
and working conditions. Today, his
innovations remain the foundation of modern
manufacturing, proving that sometimes, the
greatest revolutions come not from
invention, but from reinvention.
|