By Bryan Cady & Wayne Ashton
The Art of Fixing a Model T
Ask any Model T enthusiast how to fix one, and you’ll get a dozen different
answers - some practical, some bordering on folklore. With over a century under
its belt, Henry Ford’s revolutionary machine has gathered more myths, legends,
and mechanical wisdom than any other American car.
Even in its heyday, there were those who could fix a Model T and those who
understood a Model T. E.B. White, the beloved author of Charlotte’s Web, once
described it best: among the countless backyard mechanics attempting their own
questionable repairs, a rare few “heaven-sent” experts could truly make a Model
T sing.
White had firsthand experience with such a mechanic back in the early 1920s.
Just as he was about to board a ferry on the Columbia River in Washington, his
Model T gave out. Fortunately, the ferry captain, a former Ford garage mechanic,
saw the breakdown as an exciting diversion from his routine. With the kind of
skill that sets real experts apart, the captain got White’s car running again.
A Modern-Day Breakdown
Fast forward to today, and a similar story played out for Bryan Cady of Albany,
New York. Bryan’s pride and joy is a 1922 Ford Model T boattail speedster. While
its sleek, race-inspired bodywork hides mostly stock internals, it recently
developed a worrying problem: the high-speed band in the transmission started
slipping.
Adjusting it should have been simple. But after a test drive, something went
terribly wrong. Bryan limped home, the car groaning with an ominous mechanical
racket.
“At first, I thought it was the transmission,” Bryan admitted. But his friend
Wayne Ashton, a seasoned Model T expert from Staatsburg, New York, had a
different theory. “The torque tube acts like a trumpet,” Wayne explained. “It
amplifies and funnels noise to the transmission.”
Wayne had seen it all before. With the calm confidence of a man who’s torn down
more than a few Model T rear ends, he declared, “This is probably the tenth one
I’ve done. Five of mine, five for friends. They’re all the same!”
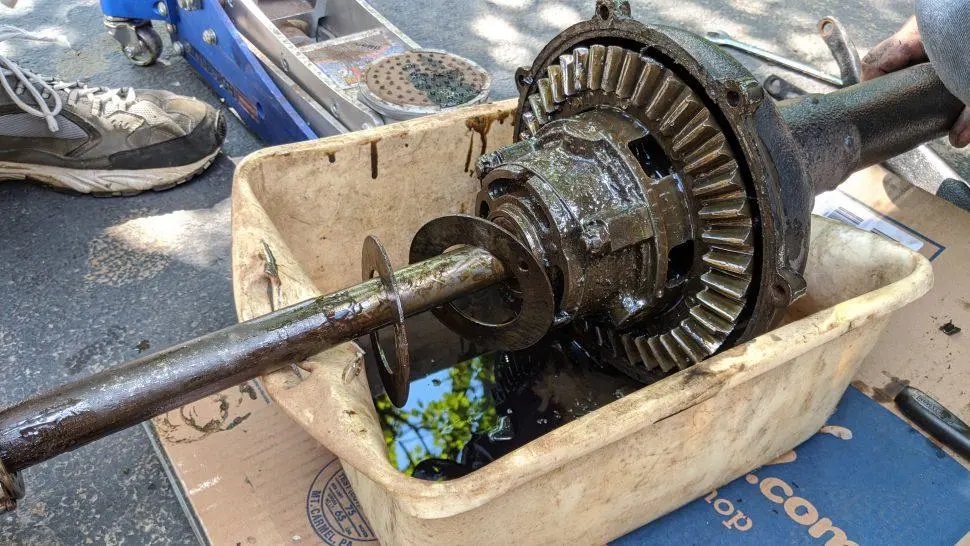
The Beauty of Simplicity
One of the joys of the Model T is its mechanical simplicity. While modern cars
demand expensive diagnostic tools, a Model T invites hands-on tinkering. By the
time the author arrived to document the repair, Wayne and Bryan had already
pulled the rear axle and torque tube - an operation that took a mere 30 minutes.
During the process, they discovered another issue: the rear axle nuts hadn’t
been properly torqued down. A small oversight, but one that could have led to a
catastrophic failure. This time, they’d be reinstalled with the proper 100 lb-ft
of torque.
Next came the moment of truth. With the axle separated, Bryan and Wayne tested
for resistance, searching for the source of the grinding noise. What they found
was bad news: a sharp catch in the driveshaft and gouged metal on the ring gear.
On a modern car, this would be a disaster. But a Model T? “You can fix most of
this stuff on the side of the road,” Wayne shrugged.
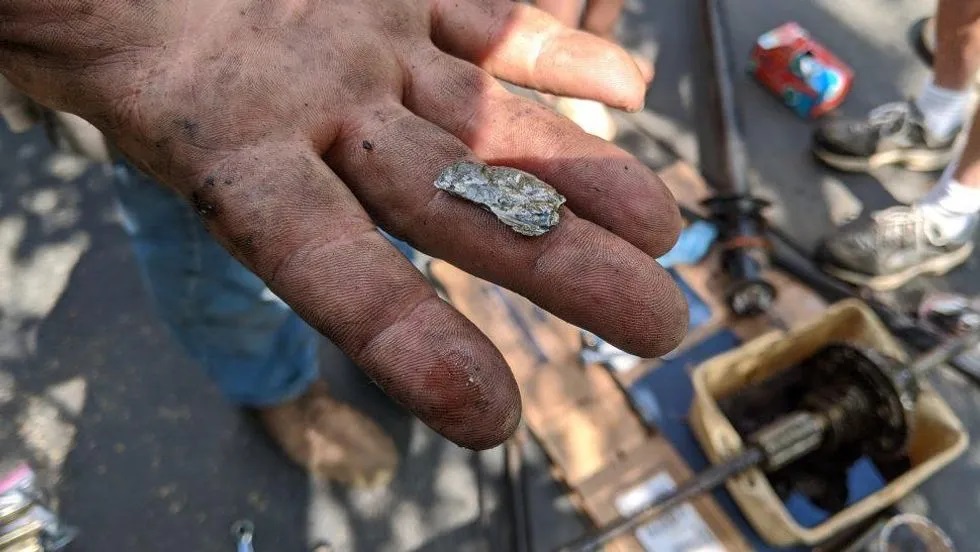
Lessons from History
In 1909, Ford famously won (and was later disqualified from winning) the Ocean
to Ocean Automobile Endurance Contest. The reason? Ford’s extensive dealer
network had given the Model T racers unauthorized support, including an entirely
new engine.
Today, official Ford support is long gone, but the massive enthusiast network
fills the gap. Model T road trips are still possible, thanks to organizations
that publish directories of fellow owners willing to lend a hand. Planning a
long journey in a T? Best to map your route around these friendly pit stops.
Wayne, taking a playful jab at Bryan’s modified speedster, had another bit of
advice: the more stock a Model T, the more reliable it is. Ford’s original
design was overbuilt and under-stressed, making it possible for enthusiasts to
push these cars far beyond their intended limits. But that extra stress comes at
a cost - hopped-up Ts cruising at 55 mph need more upkeep than those puttering
along at 35.
Ironically, Bryan’s failure wasn’t caused by modifications - it was a weak link in
the original design.
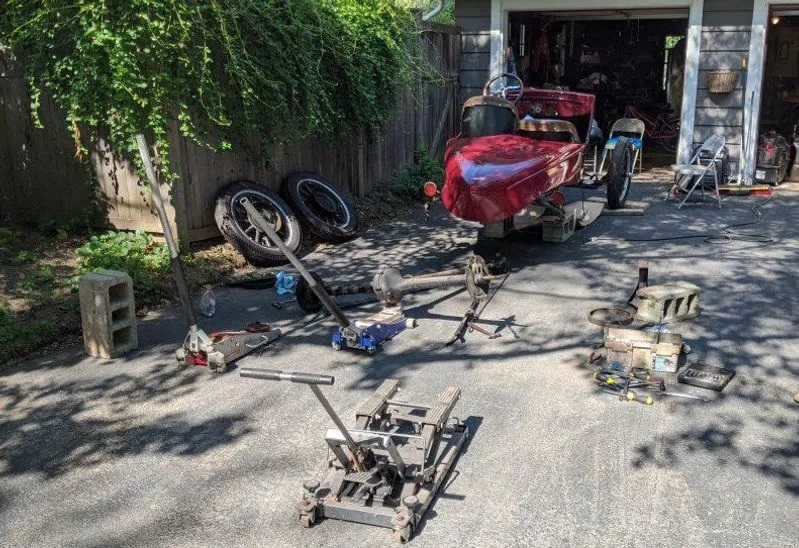
The Culprit: A Century-Old
Shortcut
One thing all Model T experts agree on? If you’re still running the original
babbitt thrust washers in the rear axle, replace them immediately.
In an effort to streamline production and reduce costs, Ford used soft babbitt
metal in the washers. While this allowed for quick assembly (the washers wore in
on their own), it wasn’t a long-term solution. After nearly a century, these
washers inevitably fail, turning into metallic shrapnel inside the rear axle.
And that’s exactly what happened to Bryan’s car. The babbitt washers finally
gave out, allowing the axles to shift and the ring gear to jump a tooth on the
pinion. Metal fragments filled the axle housing, and the gears took a beating
from the misalignment.
Wayne delivered the verdict: a complete rear axle teardown, deep cleaning, and
full rebuild - this time with proper brass thrust washers.
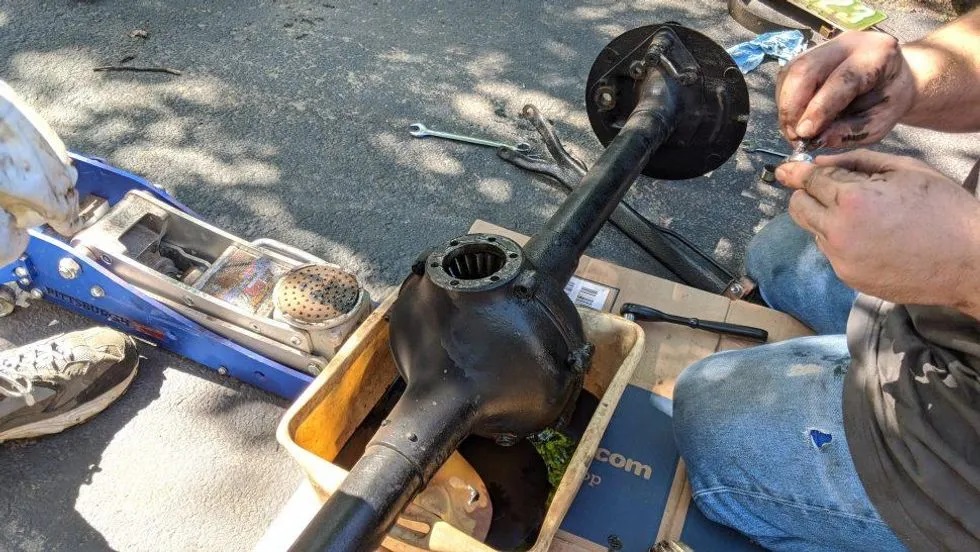
The Road Ahead
Disassembling a Model T axle isn’t difficult, but when a car has been sitting
for decades, it takes some muscle and ingenuity. With plenty of sweat (but
thankfully no blood or tears), the axle finally came apart.
The catch in the driveshaft? Just some rust. A relief, considering the bigger
issues already at hand.
Once Bryan’s replacement parts arrive, the team will be back in action,
reassembling the axle with stronger components. The brass thrust washers will
need a little fine-tuning to fit, but nothing that a dedicated driveway mechanic
can’t handle.
As always with the Model T, fixing it is part of the adventure. And thanks to
the right mix of experience, enthusiasm, and good old-fashioned mechanical
intuition, this flivver will soon be back on the road where it belongs.